Aliaje speciale - salut student!
aliaje antifricțiune sunt numite, servesc la fabricarea de piese de mașini frecare ușor schimbabile și să contribuie la reducerea frecării și piese de uzură.
fabricat cu ușurință ca parte uzură a antifrictiune aliaj (garnituri, rulmenti); materiale pentru aceste elemente ar trebui să aibă astfel de calități care, atunci când este purtat în contact cu ei partea lor greu de înlocuit al aparatului pentru a evita escoriații. Acest lucru este posibil numai în cazul în care piesele glisante sunt realizate din materiale diferite, cele mai valoroase materiale părți trebuie să fie mai greu decât materialul din care este confecționat elementul ușor schimbabil: prin urmare, duritatea aliaj antifricțiune ar trebui să fie mai mică decât duritatea revistei arborelui.
Pe de altă parte, un aliaj antifricțiune trebuie să fie, de asemenea, suficient de puternic pentru a rezista la sarcina ce acționează pe ea.
În plus, este necesar să se aliaj antifricțiune are suficientă plasticitate pentru a permite unui arbore de rulare în perioada cervix, asigurând astfel distribuția sarcinii uniform în diferite puncte ale suprafețelor de frecare.
În cele din urmă, un bun material anti-frecare ar trebui sa „hold“ lubrifiant T. E. Țineți un strat subțire de lubrifiant pe întreg planul de contact al pieselor frecare.
Pentru a satisface aceste cerințe diverse și aliaje antifrictiune parțial opuse trebuie să fie uniforme în structura și constau dintr-o masă plastică cu inclusă în acesta un hard granule de material.
Ca un aliaj tipic anti-frecare poate indica un aliaj cu un nume standard, B-83 a cărui structură constă dintr-o masă plastică din soluția solidă de antimoniu și staniu, cu solide compuși chimici SNSB (cuburi) și Cu3 Sn (ace) (fig. 152).
Ductilitatea aliajului prin prezența soluției solide, duritatea și - cristalele de compuși chimici numite mai sus. Buna retenție de lubrifiant pe suprafețele de frecare sunt realizate prin diferite grade de abraziune a suprafeței metalice; masa din plastic a declanșat cristale solide mai rapid, astfel încât, la suprafețele de frecare sunt formate microcanalele care se vor mișca liber și reținut lubrifiantul.
aliaje antifrictiune pot fi împărțite în trei grupe principale: galben, alb și negru aliaje antifricțiune; Aceasta se referă la primul bronz, la al doilea - Babbite a treia - fonte antifrictiune.
calitate de bronz anti-frecare sunt cauzate de duritatea inegală a componentelor individuale ale structurii sale. Bearings utilizate pentru bronz staniu conține în mod tipic mai puțin de 13,9%; duritate mai mică într-un astfel de material va avea o axa bogata in cupru - mult dendritele și - o dendrite staniu secțiuni mezhduosnye cu cristale incluse în aceasta a unui compus.
calitate corespunzătoare obținute în lagăre de bronz în timpul turnării în forme metalice (răcire rapidă).
FIG. 153 dat microstructură rulment din bronz, conținând aproximativ 10% staniu. Bronz este utilizat ca material antifrictiune la sarcini specifice ridicate pe arborele de lagăr și un număr mic de rotații, de exemplu, în mori de laminare.
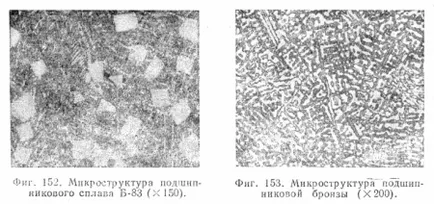
Albe aliaje antifricțiune, în funcție de metalul predominant în structura lor pot fi împărțite în babbitt cu staniu, plumb, zinc, aluminiu sau bază de magneziu.
Babbite plumb pe baza proprietăților de puțin Babbitt inferior din staniu, dar acesta din urmă este mai ieftin; acestea sunt utilizate în valorile medii ale portanța specifice și numărul mediu de rotații ale arborelui. FIG. 154 dat babbitt microstructură cu o bază de plumb. Cristale luminoase pătrate sunt compus chimic SNSB, ace, asteriscuri - Cu3 Sn, porțiunea întunecată reprezintă plumb eutectica și staniu.
In ultimii ani, o proliferare pe bază de plumb metalic babbitt cu o cantitate mică de calciu și sodiu. Acestea includ babbit sodiu-calciu BK, concepute pentru a umple rulmenții mecanismelor cu presiune specifică maximă de 200 kg / cm 2. Structura astfel babbitt prezentată în fig. 155
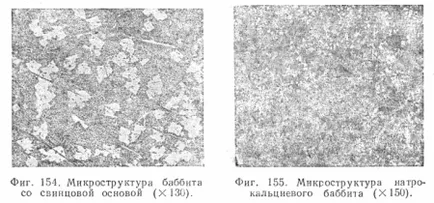
Ele sunt, de asemenea, încep să vină în utilizarea ca aliaje antifricțiune cu zinc, aluminiu și baza de magneziu.
În ultimii ani, ca înlocuitori ai aliajelor antifrictiune galben începe să se aplice fonte (de exemplu, fonta). De la manșon și garnituri de lucru, de preferință, sub sarcini statice sau dinamice antifrictiune fier preparate sunt mici. La selectarea unui aliaj de rulment ghidat de condițiile de muncă sale, proprietățile de aliaj și costul său.
Prima lucrare de cercetare în domeniul teoriei și de aplicare industrială a aliajelor antifricțiune aparțin prof. Anatoliyu Mihaylovichu Bochvaru.
Aliaje de lipit numite metale sau aliaje care sunt folosite pentru a uni două bucăți de metal.
Metalul sau aliajul numai în caz pot fi îmbinate în siguranță pentru a se asocia bucăți de alte metale, în cazul în care fiecare dintre ele este capabilă să formeze un aliaj.
metalic Solder este introdus între piesele îmbinate în stare topită; vine în contact cu obiectele materiale prin lipire, lipire se dizolvă, și în timpul solidificării legăturilor lipite obiecte în unitate solidă.
FIG. 156 este dată o imagine schematică a îmbinării tăiate format prin lipire.
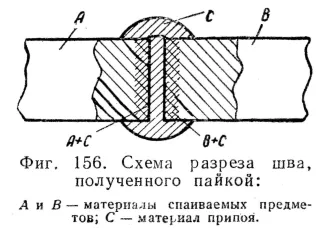
Temperatura de topire de lipire trebuie să fie puțin mai mică decât temperatura de topire a materialului sudat obiectelor, deoarece în caz contrar, obiectele pot fi lipite automat în timpul lipirii stricate.
Pentru a fi în măsură să dizolve elementele de lipire materiale în suduri topit este necesar ca suprafața lor erau destul de curate. Pentru aceasta lipit de lipire a văzut suprafața rotundă și supus curățării chimice. Substanțele utilizate pentru lipit lipire pentru a curăța suprafețele de oxizi, numite baițuri. Deoarece baițuri folosit acid clorhidric, clorura de amoniu, clorura de zinc, etc. Atunci când un agent de curățare a suprafețelor nu curge prin lipire, dar rămâne pe ele ca un strat subțire, protejează suprafața noii oxidare în contact cu aerul, se numește flux .; utilizată ca un flux, de exemplu, borax.
Deoarece temperatura de lipire de topire pentru a obține o sudură bun trebuie să se apropie cât mai aproape posibil de temperatura de topire a materialului sudat obiectele rămase oarecum dedesubt, pentru lipire diferite materiale sunt aliaje de lipit diferite.
În funcție de punctul de topire al lipiri și separate la lipire fuzibil refractar cu punct de topire scăzut, precum și de obicei are o rezistență relativ scăzută, ele sunt numite slabe și refractar - puternic.
Alcătuirea lipiri alamă tare fluctuează într-o medie de 36- 65% Cu și 35-64% Zn; punctele lor de topire variază de la 800 până la 900 °. Aceste aliaje de lipit utilizate în mod obișnuit pentru aliaje de cupru de lipit; Cu cât sunt mai cupru în materialul supus produselor de lipit, cu atât mai puternică trebuie să fie de lipire.
Pentru lipire de fier și oțel este bun argint lipire nichel (cupru-nichel aliaj). Aluminiu se pretează bine la diferite aliaje de lipit de cupru și staniu; plumb din cauza solubilitate scăzută în aluminiu nu este potrivit pentru lipirea acesteia din urmă. Compoziția din aliaje de lipit și de aluminiu este, de asemenea, adăugat la lipirea aluminiului.
Ca lipire slab utilizate din aliaje de staniu și plumb. Cele mai multe dintre aceste aliaje de topire scăzut, cunoscut sub numele de tretnik are o compoziție eutectică: 63% Sn și 37% Pb; punctul său de topire este de 182 °.
Pentru a mări duritatea lipiri pulmonare administrate, uneori, o cantitate mică de antimoniu.
Adăugarea de bismut la lipire staniu-plumb scade foarte mult temperatura de topire din urmă: de exemplu, compoziția de lipire de 15,5% Sn; 32% Pb și 52,5% Bi se topește la 96 °; lipire fuzibil special bismut utilizate în timpul sudurii staniu și aliaje de plumb.
În descrierea metodelor pentru producerea aliajelor sa spus că este posibil să se obțină aliaje, în special, presarea componentelor amestecului pulbere.
Această metodă, cunoscută de peste o sută de ani, a fost recent dezvoltat pe larg sub denumirea de metalurgia pulberilor și a aliajelor produse prin presare, am început să numim sau pulbere metalică ca proces de pulbere de metal de sinterizare este similar cu procesul de sinterizare ceramice materiale. Motivul pentru care a cauzat dezvoltarea acestei metode este posibilitatea de a produce în masă o pulbere de presare în matrițe, din care se poate obține produsul finit, precum și capacitatea de a primi produse din metale nerasplavlyaemyh (de exemplu - tungsten) și, în final, pentru a crea produse cu porozitate mare distribuită uniform.
Pulberea metalică poate fi considerată ca un corp cu un contact incomplet între particulele sale constitutive, în timp ce într-un contact metalic continuu se produce pe întreaga suprafață a boabelor. Suprafața de contact a particulelor în masa de pulbere nu depășește 0,001% din suprafața totală a particulelor. Funcționarea la primirea produsului pulbere este redusă pentru a mări contactul dintre particulele sale. rezistență îmbunătățită celulozei, precum și toate proprietățile sale mecanice Odată cu creșterea suprafeței de contact. Acest lucru se realizează prin efecte mecanice și termice asupra masei de pulbere.
Prepararea metalurgia pulberilor compus din următoarele etape: a) furnizarea de pulbere metalică, b) comprimarea amestecului de pulberi în matrițe, produse fabricate mucegai corespunzătoare, c) încălzirea masei compactate la o temperatură situată puțin sub punctul de topire, prin care sinterizează masa de aliaj .
În prezent, operația de presare este uneori combinat cu sinterizare folosind presare la cald.
Dacă pulberea de metal pulbere dintr-un material nemetalic adăugat, obținut prin comprimare urmată de sinterizare un material numit cermet aliaj.
Prin metalurgia pulberilor, în unele cazuri, a simplifica și de a reduce procesele tehnologice pentru producerea de forme complexe și dimensiuni precise; în unele cazuri, metalurgia pulberilor și este singura cale, de exemplu, la fabricarea materialelor foarte refractare.
Metalurgia pulberilor utilizate la fabricarea uneltelor (lame din metal dur), piese de mici mașini de formă complexă, părți de echipamente electrice și electronice, poroase rulmenți cu ungere de tăiere. În producția de presiune pulberi din aliaj aplicată 5-10 tone / cm2 pentru a da o contracție la 80% din volumul inițial în vrac.
Sinterizarea se realizează într-o atmosferă reducătoare. În timpul sinterizării are loc o creștere suplimentară a suprafeței de contact și, în consecință, o contracție de până la 4% din capacitatea inițială (înainte de încălzire).
aliaje de fier-metal pot fi poroase, dens și jumătate de densități (în funcție de presiunea de presare specific); sinterizate realizate la 800-1000 °; timp de 20-50 minute de sinterizare.
O serie de produse în curs de abraziune (manșon insereaza rulmenți, roți dințate), este în prezent realizată dintr-un material ceramic poros de fier, care este impregnat cu ulei, de umplere porii acestuia, și care transportă un lubrifiant în timpul funcționării.
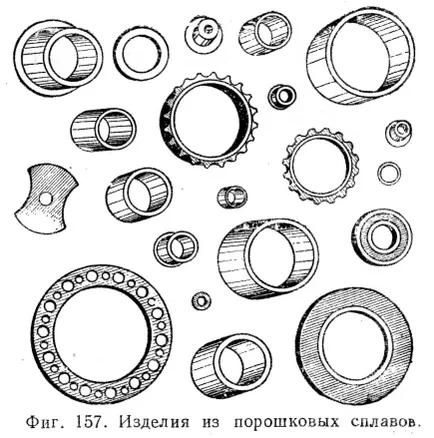
Exemplul aliaj de pulbere microstructură a fost prezentat mai sus în fig. 139; FIG. 157 prezintă produsele fabricate din aliaje de pulbere.
Descărcați hârtia: Nu trebuie să descărcați fișierele de pe serverul nostru ca DESCĂRCAREA aici
Parola pentru arhiva: privetstudent.com