Sinteza amoniacului - studopediya
• In industrie, amoniac sintetic obținut:
• la presiune redusă (10 - 15 MPa)
• ridicată (100 MPa).
• Este selectată metoda optimă de sinteză luând în considerare proprietățile fizico-chimice ale sistemului, care se bazează pe reacția chimică a azotului și hidrogenului, proprietățile materiilor prime și a produsului obținut
• sinteza catalitică a amoniacului mod posibil, atunci când temperatura de aprindere a catalizatorului (420-500 ° C) și funcționarea stabilă a catalizatorului.
• chimică și sistem tehnologic de producere a amoniacului cuprinde mai multe procese tehnologice chimice și:
• sinteza amestecului echivalent de gaz de gaz natural și abur,
• produsele porțiilor de prelucrare parafinice cu abur, și apoi cealaltă parte - oxigenul din aer pentru a trage azotul din aer pentru a lua parte la gazul de sinteză
• transformări chimice în prepararea gazului de sinteză:
Reacția gazelor naturale cu oxigenul are loc conform ecuației
și este implementat în a doua etapă conversie a gazelor naturale la gazul de sinteză pentru a produce amoniac
În prima etapă a compușilor organici cu sulf sunt hidrogenate folosind alyumokobaltmolibdenovogo sau alyumonikelmolibdenovogo catalizatorului la o temperatură de 350-400 ° C și o presiune de 2-4 MPa. În hidrogenarea următoarelor reacții:
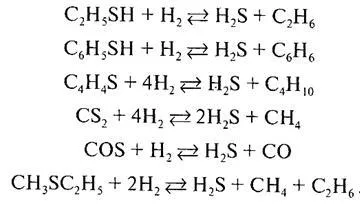
• în a doua etapă, hidrogenul sulfurat format la o temperatură de 410 0 C 390- este absorbită de un sorbent pe bază de oxid de zinc.
La o temperatură de 200 până la 500 ° C, reacția este ireversibilă și poate asigura un grad ridicat de purificare a gazului
Catalizatorii de conversie a metanului.
La scară industrială, procesul se desfășoară în prezența catalizatorilor, care nu numai că poate accelera în mod semnificativ reacția de conversie, dar un exces adecvat de oxidant pentru a exclude reacția CH4 C + 2H2.
Cea mai mare activitate catalitică în acest proces au un catalizator de nichel - alumină (Al2O3).
Catalizatorii de nichel sunt procesul de conversie a metanului este produs sub formă de tablete extrudate și inele Raschig.
Astfel, catalizatorul de brand Giap-16 are următoarea compoziție: 25% Ni0. 57% Al2O3, 10% CaO, 8% MgO.
• conversia de viață a catalizatorului în timpul utilizării normale până la trei ani sau mai mult. Activitatea lor se reduce prin acțiunea diverselor otrăvuri.
• Catalizatorii de nichel sunt cei mai sensibili la acțiunea compușilor cu sulf. Otrăvirea apare ca urmare a formării de sulfură de nichel pe suprafața catalizatorului, este inactiv pentru reacția, conversia metanului și omologii acestuia.
• otrăvire sulf a catalizatorului este aproape complet incapabil de a se regenera, în anumite condiții de temperatură atunci când se aplică într-un reactor de gaz pur. Activitatea catalizatorului Zauglerozhennogo poate fi restabilită prin tratarea cu abur.
• Gazele de eșapament sunt oxizi de azot, cantitatea de care depinde în mare măsură de raportul dintre aer și gaze naturale, iar volumul adăugat la gazele rezervorului de gaze naturale și de epurare care conțin amoniac, în anumite condiții, transformându-se în oxizi de azot
• gazele de eșapament producția de amoniac purificat prin metoda de reducere catalitică la temperaturi moderate.
• agent reducător este amoniacul, care are loc prin reducerea oxizilor de azot la azot elementar prin următoarele reacții:
• Reducerea a fost efectuată la un conținut de amoniac în exces pentru a asigura un grad înalt de conversie a oxizilor.
• utilizați alyumovanadievy alyumomargantsevovanadievy și catalizatori pentru procesul de curățare,
o durată de viață de aproximativ 5 ani. Este necesară ajustarea temperaturii de proces suficient de precis (180- 320 ° C)
• amoniac de sinteză - proces ciclic, care permite să se întoarcă amestecul azotic nereacționat în producție după separarea amoniacului format din acesta
• vitezele gazelor mari, conformarea optimă regimul de temperatură, utilizarea unui amestec de acid azotic și de înaltă puritate catalizatori activi poroase asigure o mai mare productivitate a instalației de obținere a amoniacului
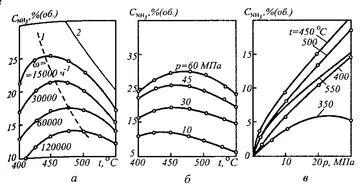
Dependența conținutului de amoniac de temperatură:
și - la diferite viteze spațiale (P = 30 MPa); b - la presiuni diferite (viteza spațială 30000 ch'1); a - de la presiunea la temperaturi diferite (viteza spațială 30000 h „1)
• Catalizatori pentru sinteza amoniacului
• ridicată Activitatea catalitică în amoniac de sinteză a metalelor exponat VI, VII și VIII ale sistemului periodic. Ei au cea mai mare activitate de Fe, Ru, Re, Os.
• În industrie au fost utilizate
catalizatori de fier, prin topirea oxizi de fier obținute cu activatori (promotori) și reducerea ulterioară a oxizilor de fier.
Ca activator utilizat oxizii acizi și caracterul amfoter. - Al2O3, SiO2, etc. TiO2i și oxizi ai metalelor alcaline și alcalino-pământoase - K20, Na2O, CaO, MgO și altele.
• Procesul de recuperare a catalizatorului poate fi descris ecuația generală
• Într-o unitate modernă de sinteză a amoniacului este efectuată la o temperatură de 420 - 500 ° C și o presiune de 32 MPa; WHSV 25 103ch -1;
• Schema de sinteză a amoniacului la presiune medie include o conversie în două trepte de metan cu abur și aer atmosferic apoi cu oxigen
După conversia CO de temperatură înaltă este realizată prin curățare monoetanolamina SO2i purificarea finală a CO și SO2kataliticheskim hidrogenare (metanare).
Următorul este sinteza amoniacului, separarea de gazul de sinteză, pentru a reduce conținutul de impurități și metan inert în gazul de sinteză la 14 - 18%.
gaz de sinteză după epurarea este supus reformei primare. Din gazul recuperat de amoniac de purjare și gazele de purjare în amestec cu un rezervor destinat incinerării în unitatea de conversie a metanului. Schema de trafic fluxuri în CTD pentru sinteza amoniacului, prezentat în Fig.
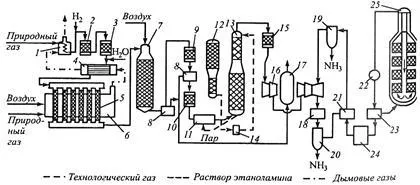
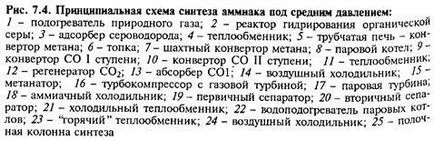
• gaze naturale sub o presiune de 4 MPa după purificarea de compuși cu sulf sunt amestecate cu abur într-un raport de 3,7. 1, preîncălzită într-un schimbător de căldură din gazele de eșapament și este direcționată în convertorul tubular, încălzit prin arderea gazelor naturale.
• Conversia metanului cu abur pentru a forma monoxid de carbon și hidrogen se realizează pe un catalizator de nichel la 800 - 850 ° C
• conversia suplimentară de metan se produce oxigen atmosferic la 900 - 1000 ° C și raportul de aer. gaz = 0,8. 1.
• De la gaz de convertizor siloz intră în cazanul recuperator de căldură unde aburul se obține cu parametri înalți (10 MPa și 480 ° C), dirijate în compresor centrifugal cu turbină și o pompă de înaltă presiune.
• Din gazul de sinteză cazan recuperator este alimentat la o conversie în două etape de oxid de carbon - primul convertor, în prima etapă pe catalizator temperatură srednetem-fier-crom, la o temperatură de 430 -470 ° C și apoi o a doua etapă în convertizor, la un catalizator de joasă tsinkhromomednom temperatură la 200 - 260 ° C .
• Între prima și a doua etape de conversie Hrsg instalate.
• scruber, irigate cu o soluție de monoetanolamină, unde la 30 la - 40 ° C, gazul de curățare din CO2
• Unitatea principală aparat de sinteză a amoniacului - coloana de sinteză
• Coloana este înălțimea cilindrului de circa 32 m și un diametru de 2,4 m,
• fluxul principal de gaz intră în coloana din partea de jos, trece prin spațiul inelar dintre garnitura de tubaje și carcasa 3 și cutia catalizatorului intră în partea de carcasă a schimbătorului de căldură 6. Gazul de sinteză este încălzită de gazul convertit la 420-440 ° C și trece succesiv patru pat de catalizator, între care servit gaz rece ocolitor. După al patrulea pat de catalizator un amestec gazos la 500-575 ° C, situată de-a lungul conductei centrale 2, trece prin tuburile schimbătorului de căldură 6, răcit la 320 - 350 ° C, și iese din coloană.