rezistența termică a metalelor
materiale rezistente la căldură și rezistente la căldură
oteluri si aliaje rezistente la căldură utilizate pentru producerea de piese de cazane, turbine cu gaz, motoare cu reacție, rachete, dispozitive nucleare, și altele. Funcționează la temperaturi ridicate.
O creștere a temperaturii reduce semnificativ proprietățile mecanice. Trebuie amintit că, în cazul în care temperatura ridicată de metal de sarcină tensiune permanentă, chiar sub punctul de randament la această temperatură și se menține sub sarcină pentru o lungă perioadă de timp, metalul în timpul acțiunii de temperatură și de încărcare se va forma o anumită viteză. Acest fenomen se numește fluaj sau târî. Dezvoltarea târî poate duce la distrugerea metalului.
Rezistența la temperaturi ridicate și fractură fluaj metalice sub rezistență la căldură pe termen lung prevăzut încărcarea. Rezistența la căldură este caracterizată printr-o fluaj condițional capelă și randamentul rezistență pe termen lung.
Fenomenul fluaj se observă atunci când temperatura de funcționare este peste temperatura de recristalizare, tensiunea de lucru peste limita elastică.
Rezistența la căldură depinde în principal de temperatura de topire metalului. Metalul mai mare de temperatura de topire, mai mare temperatura de recristalizare. Următoarea relație există între aceste temperaturi:
unde # 945; = 0,3 ... 0,4 pentru metale pure comercial, # 945; = 0,6 ... 0,8 pentru aliaje.
Sub Capela conventionala dau seama stresului fluajul este setat pentru testul la o temperatură dată este o alungire predeterminată a probei, sau o rată predeterminată de deformare (fluaj).
Fluajul este creșterea lentă în deformare plastică sub acțiunea tensiunilor mai puțin decât efortul de curgere. O dependență tipică de deformare asupra timpului de încărcare este prezentată în Fig. 1.
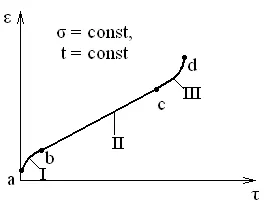
Fig. 1. Curba de fluaj: I - etapa inconstant; II - etapa de echilibru; III - etapa distrugere
Curba Fluaj constă din trei secțiuni. Etapa I așa-numita deformare la fluaj tranzitorie este diferit rata de amortizare progresivă la o anumită valoare constantă. Etapa II - fluaj constantă - caracterizată printr-o rată constantă de tulpină. In etapa fracturii III- pas - tulpina creste rata pana fractura. De regulă, este de scurtă durată și părți inacceptabile.
târî la tracțiune notat # 963; și indici numerici. De exemplu, # 963; 700 0,2 / 100 este limita de deformare la fluaj la internare la 0,2% timp de 100 de ore. La testul la 700 C. În cazul determinării rezistența la fluaj este notat cu litera # 963; două indexate numeric. Subscriptului indică o rată predeterminată fluaj (% / h), un superscript - temperatura de testare, C O; așa, # 963; 600 10 -5 - fluaj rată limită de fluaj 1 * 10 -5% / h la 600 ° C
rezistență rupere la tracțiune, adică, cel mai mare stres provocând distrugerea metalului într-un moment dat, la o temperatură constantă, denota # 963; două indexate numeric. așa # 963; Aceasta înseamnă culoar 700 1000 rezistență rupere de 1000 h. La 700 ° C
Spori rezistența termică este realizată prin doparea soluției solide, ceea ce duce la o creștere a energiei de legătură între atomii, prin procese de difuzie și de auto-difuzie sunt intarziate, iar temperatura crește recristalizare, creând un aliaj de structură specială constând din intercalat în principal soluție și limita granulei dispersată din carbură solidă și în special faze intermetalici. Această structură este obținută prin călire la temperaturi ridicate și îmbătrânire ulterioară. Prezența unui exces de faze disperse uniform distribuite complică deformare plastică la temperaturi ridicate. Cu cât bobul, cea mai mare rezistență la căldură.
Superaliaje pentru utilizare la temperaturi ridicate (până la 700 - 950ºC), sunt pe bază de fier, nichel și cobalt, și să lucreze la temperaturi mai ridicate (până la 1200-1500 ° C) - pe bază de crom, molibden și alte metale refractare .
Oțeluri rezistente la temperaturi de operare sunt 500-750 C. La temperaturi cuprinse între O și 600 O C folosesc adesea pe bază de oțel # 945, soluție solidă, în timp ce la temperaturi mai ridicate - pe baza # 947, soluție solidă cu o rețea cubică cu fețe centrate.
Pentru fabricarea pieselor și a componentelor de centrale electrice cu încărcare ușoară de lucru la temperaturi mai mari de 500-580 ° C, folosind oțel perlitice cu emisii reduse de carbon care conține cel puțin 1% crom, molibden și vanadiu. Aceste elemente, creșterea temperaturii de recristalizare din ferită și proces de difuziune obstrucționează, crește rezistența termică a oțelului.
Pentru fabricarea de piese cazane care funcționează la 510 C și o presiune de 1000-1100 MPa, este folosit un oțel 15HM sau 12H1MF mai refractare. Oțel 12H1MF manipulate în mod satisfăcător și sudate prin presiune. După normalizarea 960-980 ° C și călire la 740 C. Pe rezistența la fluaj a oțelului # 963; 560 10 -4 = 85 MPa; Limita rezistența la fluaj # 963; 560 10 4 = 140 MPa.
Temperaturile de lucru ale acestor oțeluri pot ajunge la 600-620 O C
4. oțelurile austenitice (GOST 5632-72)
oțel austenitic și din material plastic sunt sudate bine, dar tăierea lor de prelucrare dificil.
oțel austenitic conform metodei călire sunt împărțite în trei grupe:
1. Soluțiile solide care conțin relativ puține elemente de aliere;
2. Soluția solidă cu durificare carbid. În acest caz, faza de armare poate fi un primar (TiC, VC, ZrC, Nbc etc.) și carburile secundare (M7 C3 M23 C6 M6 C ..) Eliberat din soluția solidă;
3. Soluțiile solide cu întărire. Intermetalic Durificarea fază în aceste oțeluri este # 947; tip Ti Ni3 faze de, Ni3 Al, Ni3 Nb și altele.
Intemetallidnym durificarea oțelului cu mai rezistent decât oțelul cu durificare carbura de căldură.
soluții solide de structură din oțel rezistent la căldură austenitic (de exemplu, 09H14N16B și 09H14N18V2BR) concepute să funcționeze la 600-700 ° C, acestea sunt folosite după întărirea 1100-1,160 C O în apă sau în aer.
Pentru a realiza rezistență ridicată la căldură din oțel austenitic cu carbid și rigidizarea intermetalic este supus stingerea dintru 1050-1200 C O în apă, ulei sau aer pentru dizolvarea carburii și faze intermetalici în soluție solidă - austenita - obținerea, după răcire și o soluție solidă uniformă și înalt aliate maturează la 600 Despre -850 C pentru a separa fază dispersată dintr-o soluție de întărire din oțel solid.
Rezistență ridicată la temperatură oțelurile cu durificare de carbură este realizată prin introducerea unui crom-nichel sau hromonikelmargantsovisty austenita 0,3 -. 0,5% C și carburi Mo, W, V, Nb, etc. Aceste oțeluri includ, de exemplu, oțel și 45H14N14V2M 40H12N8G8MFB și oțel 40H15N7G7F2MS, în care nichel este substituit parțial cu mangan. rezistență pe termen lung # 963; 600100 oțelului a fost de 400 MPa.
Acest grup include oțel 10H11N2T3R utilizat sub formă de foi pentru piese sudate care funcționează la temperaturi de 550-750 ° C și oțel 10H11N23T3MR. rezistență pe termen lung # 963; 600100 și # 963; 700100 acestor oțeluri este de 550 - 600 și 300 - 400 MPa, respectiv.
din aliaj de oțel element superaliaje
5. rezistentă la căldură din oțel pe bază de nichel (GOST 56321-32)
-Rezistente la căldură din aliaj pe bază de nichel Nimonic apel. Aceste aliaje sunt utilizate pentru fabricarea de piese cu lungă la aproximativ 650-850 C.
Pentru obținerea rezistență ridicată la oxidare nichel aliat cu crom (20%), și pentru a îmbunătăți rezistența la căldură - titan (1,0-2,8%) și aluminiu (0,55-5,5%). În acest caz, la îmbătrânire a aliajului stins în principal # 947, soluție solidă formată intermetalice # 947; faze de [tip Ni3 (Ti, Al)] și TiC carburi și nitruri TiN, creșterea rezistenței la temperaturi ridicate. Creșterea în continuare a rezistenței la căldură se realizează prin doparea 2,0-11% aliaje Mo și 2,0-11% W, care crește temperatura de recristalizare și complică procesul de difuzie a soluției solide, determinarea fazelor exces de coagulare și recristalizare. Adaugarea la aliaje complexe de 4-16% Co contribuie la creșterea rezistenței la căldură și aliaje de ductilitate tehnologice. Pentru a consolida limitele de cereale # 947, aliaj soluție solidă este dopat cu bor și zirconiu. Ele elimină influența vătămătoare impurităților, corelându-le cu compusul refractar. Impuritățile de sulf, antimoniu, plumb și aliaje de staniu este redus rezistență la căldură și împiedică prelucrarea lor sub presiune.
Cele mai utilizate pe scară largă Nichel HN77TYUR. După stingerea dintru 1080-1120 O C are o structură constând dintr-un suprasaturat # 947; -solution cu fcc zăbrele, și, prin urmare, o rezistență mică și ductilitate ridicată admite ambutisare adâncă, îndoire și lustruire. Aliajul sudate în mod satisfăcător. După călire și îmbătrânire la 700 ° C, aliajul devine o rezistență ridicată la căldură.
HN70VMTYU aliaj larg utilizat cu bună rezistență la căldură și ductilitate suficientă la 700-800 C. On
rezistența rupere la tracțiune a aliajului # 963; 800 100 = 200 ÷ 250 MPa.
6. Metalele refractare și aliajele lor
metale refractare Chemat, punctul de topire este mai mare decât cea a fierului.
Cea mai mare valoare în domeniu sunt metale refractare Nb, Mo, Cr, Ta, și W, respectiv, cu un punct de topire de 2468, 2625, 1275, 2996 și 3410 C. On
Molibden, tungsten și crom au rezistență la temperaturi ridicate, dar acestea sunt predispuse la rupere fragilă din cauza ridicată fractură temperatură de tranziție aparență, ceea ce este deosebit de puternică creștere a impurităților interstitial C, N, H și O. după deformarea sub temperatura de recristalizare (1100-1300 ° C) pragul brittleness rece de molibden și tungsten este redusă. Niobiu și tantal, spre deosebire de tungsten și molibden - metale cu ductilitate bună și coagulare.
Molibdenul și tungsten în forma sa pură este folosită în radio și industria electronică (filament, anozi foaie, grila arcuri catozi, încălzitoare etc.), datorită secțiunii de captare transversală scăzută de neutroni și lipsa interacțiunii cu topit niobiu metale alcaline utilizate pentru fabricarea schimbătoarelor de căldură reactoare nucleare.
Rezistența la căldură de metal pur este relativ scăzută. Posedă rezistență la căldură mai mare pe baza de aliaje de metale refractare. Creșterea gradului de rezistență la căldură este realizată prin formarea unei soluții solide dopate sau soluție solidă, care în plus este întărită de carburi precipitate fine de tip ZrC, (Ti, Zr) și C și colab., Oxid (ZrO2), etc. Toate metalele refractare au o rezistență termică scăzută. Prin urmare, la temperaturi de 600-800 C O ele trebuie să fie protejate împotriva oxidării.
Pentru molibden și tungsten siliciură cel mai bine considerate acoperire prin difuziune termică (MoSi2. WSi2).
acoperiri de suprafață utilizate frecvent pentru piese de operare viață scurtă, sau o acțiune de o singură dată.
Sub rezistență la căldură (rezistență la oxidare) înseamnă capacitatea metalului de a rezista la oxidare la temperaturi ridicate. Pentru a mări rezistența la oxidare a oțelului aliat cu elemente care alterează semnificativ compoziția și structura scală. Fier la temperaturi de peste 570 C O formează trei oxid: FeO (wüstit), Fe3 O4 (magnetită), Fe2 O3 (hematita), sunt slab proteja suprafețele metalice de la expunerea la oxigen. Atunci când este administrat ca fier crom, aluminiu sau siliciu având o afinitate mai mare pentru oxigen la suprafața oxidului dens Cr2 O3 sunt formate. 2O 3. SiO2. împiedicând procesul de oxidare în continuare.
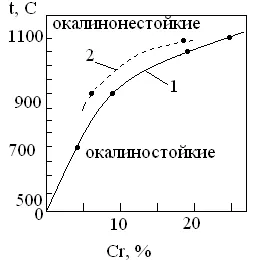
Fig. 2. Efectul de crom asupra rezistenței scalare: 1 - oțel feritic; 2 - otel austenitic
Evaluarea comparativă a rezistenței la căldură a metalelor pure asupra ratei de oxidare în aer, în intervalul de temperaturi de funcționare admisibile sunt date în tabelul. 1.
Tabelul 1. rezistență termică de metale pure
afinitate chimică mică pentru oxigen
rezistență foarte slabă căldură magneziu la temperaturi de peste 450 ° C, din cauza formării de oxid liber MgO, în care raportul de volum # 966; = 0,79. În intervalul 500-600 Rata C O Mg oxidare este în intervalul 10 -1-10 1 g / (m2 * h).
Fier Nb, Ta, Mo, oxizii W sunt dense, dar proprietățile lor protectoare se deteriorează atunci când este încălzit peste 550 C. Acest lucru se datorează faptului că acestea # 966;> 2,5, deci există tensiuni mari care cauzează oxizi de cracare. În plus, oxidul de molibden se evaporă în timpul încălzirii. Oxizii de titan și zirconiu formate la încălzire, pierde oxigen, datorită solubilității sale ridicate în metal și nu protejează împotriva oxidării ulterioare. Acest fenomen se numește oxid de degradare. La temperaturi ridicate și expunerile lungi de oxid devine chiar și în vrac. Pentru oxidarea metalului refractar la viteza aerului în intervalul 700 - O C minciună 800 oscila între 10 și 1 3 g de 10 acompaniat de / (m 2 * h).
Metale Cu, Fe, Ni, Co (vezi. Tabelul. 1), în intervalul de 500-600 C O oxidat în aer, la o rată de 10 -3-10 3 g / (m2 * h) și în intervalul 700-800 O C - de la 10 1 la 1 g / (m2 * h). rată relativ mare de oxidare a acestor metale este asociată cu un mare defect de oxizi formați în timpul încălzirii.
In timpul oxidării fierului și oțelului mai mulți oxizi cresc pe suprafață, în care compoziția chimică, structura cristalină și proprietățile de protecție diferite.
Dependența de temperatură a ratei de oxidare a fierului în aer reflectă modificările compoziției și structurii oxizilor formați pe suprafața (Fig. 3). La 560 C. La oxidarea este mai lent, deoarece oxizii formați pe suprafața Fe3 O4 și Fe2 O3 cu proprietăți bune de barieră. La încălzirea suplimentară a oxidului protector unic FeO devine mai rău cu proprietăți de barieră decât Fe3 O4 și Fe2 O3. Din acest motiv, că încălzirea admisă temperatură maximă de funcționare în aer pentru fier pur este de 560 C. Pe Prin aceasta dopare poate fi ridicată la o temperatură de 1000-1200 ° C On
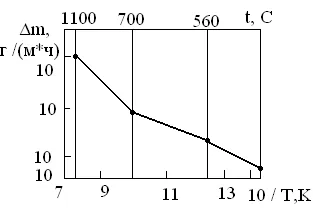
Fig. 3. Efectul temperaturii asupra vitezei de oxidare # 916; m fier în aer
Metale Al, Zn, Sn, Hb, Cr, Mn, Be (cm. Tab. 1) au o rezistență bună la căldură. Viteza de oxidare a aerului de crom în intervalul de 400 - 600 o C mai mic de 10 -6 g / (m2 * h) și în intervalul 700-800 O C este 10 -4-10 -3 g / (m 2 * h).
rezistență la căldură din aliaj de cupru industrial - alama si bronz - rezistență la căldură mai mare de cupru pur. elemente din aliaje de cupru aliere (vezi. Tabelul. 1) au o afinitate mai mare pentru oxigen decât cuprul, și cu o cantitate suficientă de oxizi proprii de formă, la încălzire, cu proprietăți de barieră mai bune decât aliajele de cupru Cu2 O. cu beriliu, aluminiu, mangan au o rezistență termică ridicată; oarecum inferioare le aliajele de cupru cu zinc, staniu și siliciu.
Titan și zirconiu aliaje absorb oxigen, astfel încât oxidul de protecție pe suprafață nu sunt formate și rezistența la căldură de titan dopare nu se îmbunătățește. aplicarea unei acoperiri rezistente la căldură, este posibil să se mărească rezistența la căldură.
Suplimentar alierea otel rezistent la siliciu căldură (2-3%) și aluminiu (până la 1-2% în oțelurile și până la 4-5%, în aliaje de mare rezistență electrică) crește temperatura de funcționare.
oțel carbon scăzut, cu un conținut mare de feritic crom devine o singură fază. În timpul funcționării prelungite la temperaturi ridicate, cristalele de ferită cresc, care este însoțită de o scădere a durității. Pentru a preveni fragilizarea oțelului aliat suplimentar cu carburi (de exemplu, Ti). Carburile împiedica creșterea boabelor de ferită. Compoziția chimică și proprietățile unor oțeluri rezistente la căldură, prezentate în tabelul. 2.
Tabelul 2. Compoziția chimică (GOST 5632-72) și proprietățile chimice ale oțelurilor rezistente la căldură
Trebuie remarcat faptul că clasa ferită de oțel și 15H25T 08H17T (în structura predomină ferită) nu este rezistent la căldură, astfel încât acestea sunt utilizate în produsele care nu se confruntă cu sarcini mari, în special tobe. 20H23N18 aliaje și 20H25N20S2 austenitică nu numai rezistente la căldură, dar rezistente la căldură. Aplicații din oțeluri rezistente la căldură și a aliajelor enumerate în tabelul. 3.
Tabelul 3. Oțeluri rezistente la căldură și aliaje utilizate electric
Temperatura de operare, C O
piese încărcate ușor de cuptoare
Muffles, ghid, piese de ventilator, benzi transportoare, transportoare cu role și cuptoare
Mufle, role de masă cu role vatra placă și alte părți de cuptoare care funcționează într-o atmosferă care conține carbon
Metalul refractar redus de căldură de rezistență - Mo, W, Ta, Nb creează mari dificultăți în utilizarea lor ca materiale rezistente la căldură. Folosirea vid și atmosferă protectoare atunci când sunt prelucrate și exploatarea metalelor refractare este, în unele cazuri mari dificultăți tehnice. Volumul acestor metale aliere nu crește rezistența la căldură, deși poate fi eficientă pentru a îmbunătăți rezistența la fluaj. Rezistență ridicată la căldură poate fi realizată prin utilizarea unui strat refractar rezistent la căldură.
3. JM Lahtin Bazele Metalurgie. - M. Metalurgie, 1988. - 320 p.