coroziunea metalelor în diferite condiții
În funcție de condițiile în care sunt operate produsele, coroziune tenĠialului electric împărțit în atmosferă, ică subterane, mor- și coroziunea în săruri topite.
Chemat eșec la coroziunea atmosferică a metalelor și aliajelor în aer umed, la temperatura ambiantă. Este cel mai frecvent tip de coroziune. Aproximativ 80% din structuri metalice operate în condiții atmosferice. coroziunea atmosferică a metalelor este, în principal de natură electrochimică și curge într-un strat subțire de rowan umiditate skondensi- pe suprafața metalică.
Factorii principali care determină viteza de coroziune într-o atmosferă, gradul de hidratare sunt suprafețe metalice coroziune contaminării și temperatură. Acești factori variază în limite largi, de exemplu, într-o mulțime atmosferă marină de săruri, în special clorură de clorură de sodiu în atmosfera zonelor industriale mult oxizi de sulf ug- leroda, azot și altele.
Prin gradul de hidratare al suprafeței metalului, următoarele tipuri de coroziune atmosferică: uscate, umede și umede.
coroziunea atmosferică uscată - este absența completă a coroziunii a peliculei de umiditate pe suprafața metalică. mecanism de coroziune metalic uscat este o interacțiune proces gaze corozive suprafață pur chimice oxidate. Aerul uscat la suprafața straturilor de oxizi metalici sunt formate, care reduc oxidarea ulterioară a metalului. Dacă există și alte gaze de aer, cum ar fi compuși cu sulf, proprietățile de film de protecție pot fi reduse, iar viteza de coroziune în legătură cu această creștere.
coroziunea atmosferică umedă are loc în prezența unui film invizibil suprafață metalică extrafin de umiditate, care este produsă în rezultatele sunt condensarea la o umiditate relativă mai mică de 100%. Prin condensarea umidității într-o astfel de atmosferă poate fi diferită:
- capilara. Capilarele, fante, lacune favorizează condensarea, deoarece acestea au un mic menise lichid concav Ar trebui
secvență, cea mai mică presiune de vapori. Odată cu scăderea razei de curbură a meniscului concav vodya- a redus presiunea de vapori saturați deasupra. Astfel, prezența capilarelor cu pereti umectabile în condensarea vaporilor de apă, sheniyu nesaturate Raportul dintre meniscului fluid plat.
- Adsorbția. Condensul apare datorită absorbției umezelii pe suprafața metalică.
- chimice. Condensul apare ca urmare a produselor sau săruri de coroziune interacțiune chimică, situate pe suprafețele de metal cu apă și este însoțită de formarea de compuși hidratate Nij. Prezența filmului soluție de sare favorizează formarea condensului, deoarece presiunea vaporilor deasupra soluției sub decât deasupra solventului pur. sare Hygro- skopichnost accelerează condensarea.
Mecanismul de coroziune a metalelor în atmosferă umedă, de preferință electrochimice. Element de lucru al mikrogalvanicheskogo coroziune afectează în mod semnificativ rezistența peliculei de umiditate pe suprafața metalului.
coroziunea atmosferică umedă - metale de coroziune în prezența pe suprafața lor o peliculă vizibilă de umiditate care curge la o umiditate relativă de aproximativ 100%. O astfel coroziunea atmosferică observată la condensarea umezelii în picături pe suprafața metalică, de asemenea, prin contact direct cu umezeala pe metal (ploaie, turnare de apă, și așa construcții. D.). aproape umed la coroziunea atmosferică coroziune galvanică cu imersiune completă a metalului în electrolit.
La rata de coroziune atmosferică afectează în mod semnificativ gradul de umiditate de suprafață, t. E. Grosimea stratului de umiditate (fig. 5.1).
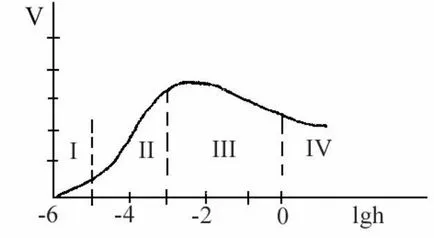
Fig. 5.1 atmosferic dependența vitezei de coroziune a logaritmului grosimii stratului de umiditate (h) pe suprafața metalică: I -
uscat; II - umed; III - umed; IV - coroziune atunci când sunt complet imersate în electrolit
Odată cu creșterea grosimii filmului umed pe viteza suprafață metalică de coroziune inițial crește brusc datorită creșterii conductivității electrice a electrolitului, iar apoi a scăzut ușor datorită ratei de descreștere de difuzie a oxigenului la suprafața metalică.
Umiditatea este unul dintre principalii factori care contribuie la formarea unui film de umiditate pe suprafața metalului. umiditate la care un film continuu de umiditate pe suprafața metalică în condensare rezultat apă PE se numește umiditatea critică. Umiditatea critică variază semnificativ în funcție de starea suprafeței metalului și compoziția atmosferei. atmosferă industrială umiditate critică este o medie de 60% (umiditate relativă). Atunci când umiditatea relativă a atmosferei peste rata critică de coroziune atmosferică crește dramatic.
Rata de coroziune atmosferică a metalelor este influențată și de compoziția filmului de umiditate, temperatura, contactul cu alte metale.
Impuritatile din aer afectează foarte mult rata de rozii atmosferice corespondenți. Compoziția filmului de umiditate pe suprafața metalică și gradul de agresiv funcției ITS a poluării aerului și natura contaminanților. Gaze Articole metal (SO2, SO3, CO2, H2S, NH3, Cl2, HCl), obținerea într-un film de umiditate pe suprafața metalică, crescând conductivitatea electrică, coroziunea NOSTA produse higroscopice acționează ca depassivatory (de exemplu, SO2,
CI1). Particulele solide (de exemplu particule de carbon), care se încadrează pe suprafața metalului, promovează adsorbția diferite gaze, condensarea umezelii în interior. Cele mai agresive sunt atmosfera industriale puternic poluate, cel mai puțin activ - (. Tabelul 5.1) Aerul continental curat și uscat.
Rata relativă coroziune sion, oțel carbon (pentru Gadsonu), scor
Industriale, puternic poluate
Viteza de coroziune atmosferică a metalelor care influențează fluctuațiile de temperatură ascuțite. Creșterea corozivitate cu trecerea de la negativ la temperaturi pozitive explică o rată de creștere a proceselor electrochimice datorită trecerii filmului de umiditate pe suprafața metalică a solid la starea de agregare lichidă. Prin reducerea temperaturii în seara și noaptea, cu umiditate relativă a aerului crește dramatic, rezultând condensarea rouă pe suprafața metalelor și creșterea coroziunii electrochimice.
Viteza de coroziune atmosferică este considerabil influențează contactul a două metale având valori diferite ale potențialelor de electrod. Atunci când se decide cu privire la admisibilitatea contactului între metale sau spla- ar trebui să fie ghidate de următoarele date. Toate metalele și spla- vă sunt împărțite în cinci grupe principale: 1 - magneziu; 2 - zinc, aluminiu, kad- mea; 3 - fier, oțel carbon, plumb, staniu; 4 - nichel, crom, Misty oțel crom, oțel crom-nichel; aliaje de cupru-nichel, cupru, CE costale - 5. Contact de metal aparținând aceluiași grup este considerat acceptabil, dar fiecare grup succesiv de metale crește coroziune a metalelor din grupul anterior.
Următoarele metode sunt utilizate pe scară largă pentru a proteja metalul de coroziune atmosferică.
- Metalele de dopaj. Pentru condițiile de funcționare nai- atmosferice pot fi considerate un dopaj mai eficient, ceea ce conduce la producerea de aliaje metalice cu un perfect produse strat protector
coroziune sau cu aliaje reduse activitate anodice. De exemplu, stânga-girovanie devin metale ușor pasivizate (crom, nichel, aluminiu, titan) sau aditivi catodului (cupru) facilitarea passivirova- coroziunii oțelului în condiții atmosferice, reduce viteza de coroziune.
- Reducerea umidității relative. Reducerea suprafeței metalice a stratului electrolitic prin reducerea dispozitivelor de conservare umiditate în tuburi sigilate cu un agent deshidratant (silicagel) conduce la o încetinire a elementelor corozive.
- Utilizarea de acoperiri de protecție. Pentru protecția împotriva rozii atmosferice utilizate pe scară largă corespondenți metalic protector (lac), din metal, oxid, fosfat și alte acoperiri.
Coroziunea subterană a structurilor metalice are loc în condiții de pochven- GUVERNAMENTAL sau sol și este, de obicei, un mecanism electrochimic. coroziune subterană predispuse fire metalice în principal de conducte, rezervoare de stocare subterane, cabluri electrice, etc .. de degradare puternică speciale observate sub acțiunea comună a curenților de sol și la sol.
Următoarele tipuri de coroziune a solului:
- Coroziunea subterane - coroziune în sol cauzată de elemente corozive care apar pe metal în locurile de contact cu suportul său rozionnoy de temelie datorită neomogenitatea structurilor metalice, neodim compoziția Nakova solului, diferențele de temperatură, umiditate și sol vozduhoprovod- structuri NOSTA în diferite zone.
- biocorrosion subterane - coroziune este cauzat microorganisme Stu zhiznedeyatelno- care acționează asupra metalului, de obicei, procesul este finalizat cu o coroziune galvanică.
- Electrocorrosion - coroziune subterană a structurilor metalice prin acțiunea șinelor curenților de scurgere electrificate corn de cale ferată pre- și alte plante industriale. Acesta este împărțit în coroziunea prin coroziune curenții vagabonzi și șocurile externe.
Umezeala conținută în sol și diverși agenți chimici, deci are o conductivitate ionică și în cele mai multe cazuri, cu excepția solurile foarte uscate, mecanismul de coroziune subteran - cerul electrochimica. Cea mai caracteristică a procesului catodic în condiții subterane yav-
doresc să înființeze depolarizare de oxigen. În soluri acide (mlăștinoase) poate suferi coroziunea și depolarizare de hidrogen.
Să considerăm un exemplu de funcționare elementului coroziv în sol (fig. 5.2).
Pentru a combate coroziunea structurilor subterane sunt larg utilizate următoarele metode:
- strat de protecție izolator. Aceasta este principala metodă de protecție. De exemplu, pentru conductele aplicate de acoperire bituminos. De asemenea acoperiri pe bază de benzi de policlorură de vinil și adezive din polietilenă utilizate.
- Protecție catodică de la o sursă de curent continuu externă sau de protecție tektornaya pro.
- mediu artificial. Pentru a proteja conducta de coroziune a solului prelucrat înconjurător metal, diferite substanțe pentru reducerea sau neutralizarea proprietăților corozive (de exemplu, prin tratare cu var sol acid). Uneori, pentru a crea un lot omogen pe întreaga lungime a conductei este umplut sol nisipos. One-Naco, această metodă este foarte consumatoare de timp și costisitoare.
metale coroziune curent vagabonzi
Coroziunea metalelor curenților de dispersie este privat, dar, practic, importantă cazul influenței câmpului electric în electrolit asupra procesului electrochimic de coroziune de metal.
Curentul electric în pământ, ramificare de la calea sa principală, numită vagului. sursă de curent de dispersie pot fi electrice căi ferate, Electrolizoare, sudori, instalarea catod, linii electrice, și altele. Luați în considerare efectul Vagus
Curenții de pe electrizat coroziune feroviar structuri subterane GUVERNAMENTALE (Fig. 5.4).
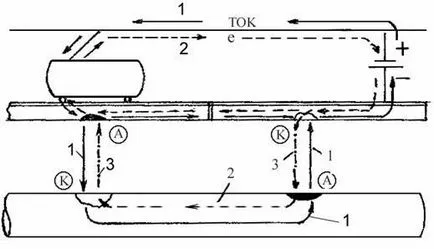
Fig. 5.4 Coroziunea conductei de curenților vagabonzi ferate electrificate: 1 - direcția mișcării curente; 2 - direcția de mișcare a electronilor;
3 - direcția de mișcare a ionilor
Atunci când fluxul de curent de tracțiune de-a lungul șinelor, care are loc cădere de tensiune, iar șinele primesc un potențial pozitiv cu privire la sol, dar izolarea imperfectă de șina sol determină curentul de scurgere în sol din jur. Cu cât este mai și rezistență mai mică la rezistivitate tranzitorie longitudinală, mai mare scurgere de curent la masă totală. substații Apropiat și conectarea punctelor de cablu la șinele de curent tarozilor, există zone de polaritate negativă constantă a șinelor, și la o distanță considerabilă de la ei - o polaritate pozitivă permanentă Noe. Care au loc în țara curenților vagabonzi, reuniți asupra structurilor metalice modul, invada și le curge prin el rom nekoto- peste, creând o zonă catod și un anod.
Particularitatea procesului coroziunii metalelor în curenților de dispersie za- constă în faptul că acesta este un proces electrolitic care se desfășoară în conformitate cu legile electrolizei. Pe părțile catodice ale construcției va continua acțiunea de recuperare a hidrogenului PE:
zone anodice - reacția de oxidare metalic:
Me + mH2O → ® Men + × + mH2O ne.
Prezența zonelor catodice și anodice clădirii este determinată de direcțiile de curent. Se trasează structuri de intrare sau în calitate de ieșire de electroni doresc să înființeze catod. Se trasează structurile actuale de ieșire sau intrare în calitate de electroni doresc să înființeze anod.
Dacă un curent electric constant, porțiunile metalice din care sunt ioni pozitivi intra în electrolit și anozii sunt podverga- sunt electrocorrosion; regiuni în care ionii pozitivi sunt transferați din electrolit în metal, catozii sunt, pe baza cărora are loc procesul de recuperare. Rata de coroziune este proporțională cu fluxul de curent. Alternarea Vagus curent korrozionnoopasen, de asemenea, dar într-o mai mică penalități Gradul decât permanentă.
Intensitatea procesului de coroziune metal curenților de dispersie sunt de obicei mult mai mare decât intensitatea coroziunii solului. Aceste două procese sunt suprapuse pe reciproc. Când această coincidență zonele anodice elemente corozive și a curenților vagabonzi conduce la creșterea coroziunii.
La suficient de mari potențiale suprima curenților de dispersie ultimul microcelulare catod curent care apar în timpul coroziunii clorhidric pochven- răspândirea microportions distrugere toate structurile din zona anodică a curenților de dispersie.
Sub acțiunea stray valorii structurilor curenților de potențialul de polarizare este deplasat spre zonele anodice în direcția pozitivă Potențialul relativ staționar în catod - negativ. Amploarea ratei de coroziune determinată de densitatea curentului de scurgere.
Aplicarea straturilor de protecție (vopsele, bitum, județe din polietilena etc.) brusc crește rezistența. Rezistența de izolație a structurilor subterane - cel mai important factor de limitare curenții zhdayuschih Blu- afectează structura. Comparativ cu clădiri prost izolate într-un curent de coroziune bine izolată scade la o sută de ori.
Solul este un conductor paralel, cum ar fi șine, și în funcție de valoarea rezistenței electrice a șinelor și sol, curentul este uneori cantități foarte mari (până la sute de amperi) se extinde de-a lungul solului. Displace- curenți care dau au o rază de până la zeci de kilometri distanță de structurile actuale purtătoare.
coroziune marină a metalelor mecanism electrochimice, în principal, cu depolarizare de oxigen. La rata de coroziune marină ajută să se refere influența compoziția apei de mare, temperatura și viteza sa, factorul mecanic suplimentar (aerare, cavitație), contactul de metale diferite, factorul biologic (ancrasare structurilor subacvatice plante marine metalice și animale de către organism). Concentrația totală de săruri din apa de mare ajunge la 4%, ceea ce afectează conductivitatea. Iod și brom acționează ca depolarizer catod suplimentar și accelerează coroziunea. Clor-ion este un depassivatorom puternic NYM, t. E. Procesul anodic accelerează coroziunea metalelor. Ce rovodorod acidifiat cu apă de mare și se leagă de ionii metalici în sulfuri solubile dure, facilitând curgerea anodice și catodice proceselor electroni electrod coroziune electrochimice. Odată cu trecerea unui curent electric prin partea subacvatice de nave și structuri offshore ia naștere elektrokorrozii lor.
O mare influență asupra vitezei de coroziune în apa de mare exercită adâncimea de scufundare. Rata de coroziune metalică scade brusc cu adâncimi de imersie clorhidric, datorită reducerii conținutului de oxigen în apă. La o adâncime de 1000 de metri există o rată minimă de coroziune, care corespunde unui atinge un conținut minim de oxigen în apa de mare.
Rata relativ ridicată de coroziune a navelor de pe linia de plutire. proces deosebit de intens fractura de metal se dezvoltă într-o zonă oarecum deasupra acestei poziții de distribuție linie. Acest lucru contribuie la îmbunătățirea accesului oxigenului, spălând peliculele protectoare de suprafață, skoe periodic umezire electrolit urmată de uscare, diferența de temperatură.
Cea mai comună metodă de protejare împotriva coroziunii metalelor în apă de mare este de a aplica acoperiri vopsea. De asemenea, utilizate sunt zinc și cadmiu acoperire ca independent sau ca un sub-strat sub vopsea. Acesta este utilizat pe scară largă electrochimica
protecția navelor și structurilor marine, precum și utilizarea unor aliaje rezistente la coroziune (de exemplu, cupru-nichel din aliaj).