Tratamentul Beam - studopediya
Caracterizarea proceselor tehnologice
Prin metode radiologice de formare a pieselor includ:
1. Tratamentul cu fascicul de electroni.
2. fascicul de lumină (laser) tratament.
3. Prelucrarea cu plasmă.
Tratamentul cu fascicul de electroni (ELO), bazat pe efectul termic al deplasarea fluxului de electroni pe materialul prelucrat care procesarea locație topește și se evaporă. O astfel de căldură intensă cauzată de faptul că energia cinetică a electronilor în mișcare sunt lovit pe suprafața piesei este aproape complet transformată în căldură, care este concentrată la locul de dimensiuni mici (mai puțin de 10 microni), se încălzește la 6000 0 C. La procesarea dimensională ca este cunoscut să apară un efect local asupra materialului prelucrat, care este prevăzut cu ELO modul flux de electroni în impulsuri cu durata impulsului ... 10-4 și 10-6 cu frecvența f = 50 ... 5000 Hz. O concentrație mare de energie, cuplată cu ELO Impulsive asigura condiții de prelucrare conform cărora suprafața piesei, la o distanță de 1 m de marginea fasciculului de electroni, este încălzit până la 3000 0 C. Acest lucru permite utilizarea ELO pentru taierea semifabricatelor, fabricarea plaselor folie de tăiere caneluri și găuri de prelucrare cu diametrul de 1 - 10 micrometri în detaliile materialelor dure. Aparate de tratament cu fascicul de electroni este prezentat în Fig. 52.
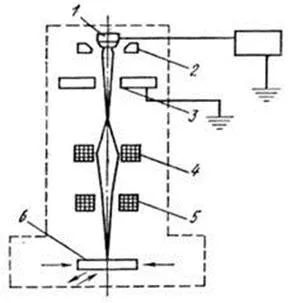
Fig. 52. Dispozitiv pentru tratament cu fascicul de electroni:
1 - pistol cu catod de electroni; 2 - electrod; 3 - un anod; 4 - lentile electromagnetice; 5 - sistem magnetic; 6 piese de prelucrat.
În instalațiile de prelucrare cu fascicul de electroni, electronii sunt simulate la catod de tun de electroni 1; sunt formate într-un electrod de fascicul 2 localizat imediat în spatele catod; accelerată de diferența de potențial dintre catod și anod 3 de circa 150 kV, iar apoi sunt concentrate într-un fascicul în obiectiv electromagnetic 4. focalizat fascicul de electroni care trece prin sistemul magnet deflexie 5, cade pe piesa de prelucrat. Prelucrarea se efectuează într-un vid de ordinul a 10 -2-10 -4 Pa.
Atunci când unitatea de procesare a pieselor dimensionale funcționează într-un mod în impulsuri cu o durată a impulsului de 10 -4-10 -6 s și o frecvență de 150-6000 Hz, oferind o încălzire locală a semifabricatului. Temperatura zonei de prelucrare a atinge circa 6000 C, și la o distanță de 1 m de la fața locului fascicul focalizat este mai mică de 300 C. Diametrul fasciculului focalizat pe zona de tratament poate fi de 10 - 400 microni, în timp ce densitatea de energie se realizează aproximativ 10 7 W / cm2.
Metoda fascicul de electroni este utilizat pentru tratarea materialelor refractare și ușor oxidabile în metale aer și aliaje de wolfram, molibden, titan, cupru, precum și nemetalice: rubin, ceramica, cuart, ferita, si materiale semiconductoare. Dimensionarea recipientului sunt utilizate pentru diametrul găurii EEPROM de 0,01 -. 1 mm, tăiere fante, tăiate părți din semifabricate din foi de-a lungul conturului foliei care primesc grile, etc. Mai mult, sudarea cu fascicul de electroni este utilizat pe scară largă pentru părți de metale reactive de topire ridicate și aliajele lor (wolfram, tantal, molibden, niobiu, zirconiu, etc.).
Fascicul de lumină (laser) de prelucrare bazată pe efectul termic al fasciculului de lumină mare de energie pe suprafața piesei. Sursa de radiații de lumină este un laser - Generator cuantic optic (laser). Crearea design-ului de lasere solide, gaz și semiconductoare. Munca lor se bazează pe principiul de a genera o emisie de lumină stimulată. Pentru prelucrare folosind radiații laser în stare solidă, un element de lucru, care este o singură tijă de cristal rubin constând din alumine, activat 0,05% crom. cu laser Ruby funcționează în modul în impulsuri, generând impulsuri de coerente monocromatice roșu de lungime de undă 0,69 microni. Fig. 53 prezintă o diagramă de rubin dispozitiv cu laser.
Fig. 53. Circuitul maserul optic:
a) Schema laserului; b) concentrarea unei scheme de fascicul laser.
Când sursa de alimentare 5 a luminii pompa 2 este iradiat de tijă rubin 1 flux puternic de lumină cu o lățime de bandă largă, care se traduce ionii de crom în stare excitată. Din această stare, ei pot reveni la starea normală, care emit fotoni de o lungime de undă de 0,69 microni. Direcția de propagare a undelor de lumină în mod aleatoriu, astfel încât interiorul cristalului sunt acele valuri ale căror direcție perpendiculară pe suprafața fețelor de capăt de tijă, iar restul dincolo de cristal. Prezența suprafețelor oglinzi capăt 3 și 4 conduce la faptul că, atunci când reflexie multiplă prin ele libere amplificate vibrații ușoare în amplitudine și putere în direcția axei tijei datorită stimulării atomilor excitați. În acest caz, un flux de valuri coerente. valuri de mișcare în interiorul rezonator va avea loc atât timp cât lumina generată nu va fi suficientă pentru ieșire prin oglindă semitransparentă 4. Pentru utilizare în procesul de a focaliza fasciculul laser (Fig. 53b).
lasere în stare solidă au de obicei o grosime relativ mică: funcționează în modul de impulsuri - puterea care nu depășește 300 wați, și în mod continuu, - până la 500 wați. Dar fasciculul laser focalizat va da o densitate de energie enormă care asigură încălzirea la o temperatură de 6000 - 8000 ° C. De exemplu, un fascicul laser cu o putere de ieșire de 20 W concentrat într-un diametru de 0,01 mm, se va asigura o densitate de energie la locul de până la 10 8 W / cm2 .
Procesarea laser este folosit pentru a coase prin și oarbe găuri, tăierea semifabricatelor în părți tăiate din semifabricate foaie material pe continuu de tăiere fante contur. piesa de prelucrat pot fi prelucrate prin această metodă din oricare dintre materialele, inclusiv cele mai solide și durabile. Acesta este utilizat pe scară largă pentru sudarea cu laser a diferitelor metale. De exemplu, raza laser cojile de sudură produc circuite integrate hibride și adaptarea la rezistența nominală a filmelor subtiri rezistive de film.
Plasma obrabotka.V Instrumentation Technology, radioapparatostroeniya și metal cu plasmă este utilizat ca un jet fierbinte narrowcasting topi capabil și vaporizează substanțial toate materialele: materialele și nu materiale. Prin proiectare, torțe de plasmă sunt împărțite în separatoare de acțiuni directe și indirecte. Fig. 54 prezintă un aparat torței cu plasmă.
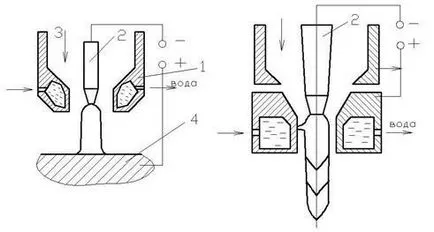
Fig.54. Aparat cu plasmă torță 1 - duză; 2 - electrod de wolfram;
3 - gaz de plasmă de intrare; 4 - articol.
Pentru plasma utilizate arc electrolitica prin care duza 1 prin gazul de plasmă este suflat 3 (argon, azot, aer sau un amestec al acestora). Puterea este furnizată de la sursa de alimentare electrică Plasmatron cu o tensiune de 200-500 V și un curent de 300-400 A. este necesară pentru stabilizarea arcului la jet fierbinte la duza nu a închis și nu se topească, precum și la un accent. Acesta este implementat de gaz cu flux axial sau pereții unei duze răcite redus.
Tratamentul cu plasmă este utilizat în procesele care necesită tăiere mare de căldură concentrată, găuri, micro piercing - și makrosvarka, acoperire, restaurare a pieselor uzate, topirea.
Surfacing strat rezistent la uzură se realizează pentru a îmbunătăți proprietățile de performanță detaliu. Astfel, se pot utiliza materiale pulverulente cu proprietăți speciale - duritate mare, rezistență ridicată la uzură, coroziune - și rezistență la căldură (oxizi de bor sau carburi, wolfram). Detaliile sunt obținute cu un nucleu de materiale de construcții ieftine și în zonele sensibile sunt proprietățile necesare. În mod semnificativ a redus costul materialelor de aliere scumpe. Grosimea stratului poate fi de mai multe mm. Tehnologia constă în aceea că materialul de acoperire este folosit ca o pastă; topește și stratul de sudură sudabile cu materialul de bază mamă. În acest caz, plasma lanterne de acțiune indirectă.
Când pulverizarea materialului de pulverizare este încălzit în plasmatron. Temperatura substratului în funcție de obiectivul sputtering poate fi variată. Straturi formate din grosime mică - de la câțiva microni la un mm. Pentru a mări aderența stratului pulverizat tind să crească gradul de acțiune chimică a acoperirii pe substrat datorită încălzirii sale sau introducerea straturilor intermediare reactive.
Utilizate pe scară largă de tăiere cu plasmă. plasma Avantaje taiere: prelucrează metale până la 100-150 mm grosime, mai mică decât lățimea de tăiere în timpul tăierii cu gaz, modificări termice cea mai bună suprafață mai mică. Viteza de 0,5-1,5 cm / s, în funcție de grosimea stratului. Plasma torțe de plasmă de tăiere sunt utilizate în acțiune directă. gaz plasma - argon, azot, hidrogen sau aer. Când microplasma tăiere curent 50-100 O grosime de taiere de 8 mm, lățimea tăiate până la 1 mm.
Fig. 55 prezintă o diagramă de tăiere cu plasmă.
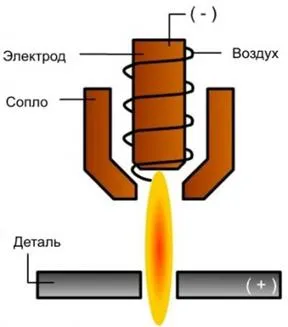
Fig. 55. Schema de tăiere cu plasmă.
Decupare cu plasmă este de departe metoda cea mai productivă a oțelurilor de taiere termica si metale. Acest tip de tratament presupune utilizarea materialelor în torța cu plasmă ca instrument în locul cuțitului. Pentru jet de plasmă utilizând gaze active (oxigen, aer) și inactive (vapori de apă, azot, argon, hidrogen). Pentru tăierea metalelor feroase sunt utilizate în principal gazele active, pentru metale și aliaje neferoase - inactive.
Decupare cu plasmă permite lucrul cu orice metale (oțel inoxidabil, aliaje de aluminiu, cupru, etc.); Fără proces de tăiere cu plasmă astăzi nu se poate face nici una din întreprinderile angajate în tăiere de metal pe o scară mică sau mare. Principalul avantaj al acestei metode - de mare viteză și eficiență. Calitatea tăiat, această tehnologie este doar ușor inferior numai de tăiere cu laser, dar uneori să depășească performanțele sale economice și posibilități mai largi, în special în legătură cu grosimea maximă de tăiere a metalelor.
Avantajele taierii cu plasma:
- economisind timpul de client, datorită vitezei mari de execuție a lucrărilor;
- încălzire mică și localizată a piesei de tăiat, care exclude deformarea termică;
- puritate ridicată și calitatea suprafeței de tăiere;
- siguranța procesului datorită absenței buteliilor cu gaze combustibile și explozive;
- Numărul minim de bavuri și zgură.