Tipuri de soluții solide
Titlul lucrării: Tipuri de soluții solide
Zona de subiect: Fizică
Descriere: Descrie tipurile de soluții solide. Dă exemple. Dă duritate. Ce metode de măsurare a durității metalelor și aliajelor? Descrie-le. Desenați diagrama de fază a carburii de fier-fier, selectați compilarea structurală.
Dimensiune fișier: 227.09 KB
Munca Descarcate: 342 de persoane.
1. Descrie tipurile de soluții solide. Dă exemple.
2. Definiți duritate. Ce metode de măsurare a durității metalelor și aliajelor? Descrie-le.
3. Desenați diagrama de fază a carburii de fier-fier, selectați structural co-stavlyayuschie în toate domeniile diagramei descriu constructul de transformare și curba de răcire (folosind regula de fază) pentru un aliaj care conține 2,2% C. Care este structura aliajului la temperatura camerei și modul în care un astfel de aliaj este numit?
4. Desenați diagrama de transformare izotermice pentru U8 otel austenitei. Nana-l sită modul de procesare a curba izotermă, ofera o duritate de 150 HB. Indicați modul în care acest lucru se numește și ce structură se obține în acest caz.
5. Cu diagrama de faza de fier-cementita justifica alegerea tratamentului termic aplicat pentru a elimina cementita din plasă de oțel hypereutectoid. Definiți modul de procesare selectat și descrie transformările care au loc în timpul încălzirii și răcirii.
Soluțiile solide sunt numite faze, în care una dintre componentele aliajului păstrează rețelelor cristaline, și alți atomi (sau alte componente) sunt aranjate în rețeaua primului component (solvent), modificarea dimensiunilor sale (perioadele). Astfel, soluția solidă, co-standing a două sau mai multe componente, are un tip grilaj și este o singură fază.
Există soluții solide și soluții solide de substituție. În formarea soluțiilor solide ale atomilor component B dizolvate sunt aranjate între solvent A atomii rețelelor cristaline. În formarea soluțiilor substitutionali solide ale atomilor component B dizolvat înlocuiți unele dintre atomii de solvent (component A) în zabrele sa cristalină.
Figura 1 # 150; Soluțiile solide: și # 150; substituție, b # 150; introducere
Deoarece dimensiunile atomilor solut de mărimi diferite ale atomilor de solvent, formarea soluției solide este însoțită de deformarea rețelei cristaline a solventului.
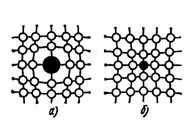
Figura 2 # 150; Distorsiunea în rețeaua cristalină a soluțiilor solide substitutionali:
și # 150; atom atom solut mai mult solvent
b # 150; atom atom solut mai puțin solvent
soluții solide substitutionali poate fi limitată și solubilitate nelimitată. În soluții solide cu solubilitate limitată concentrație solutului este posibilă în anumite limite.
În soluții solide cu solubilitate nelimitată poate fi orice concentrație de solut (0 până la 100%). Soluțiile solide cu solubilitate nelimitată formată în următoarele condiții: 1) la componentele trebuie să fie același tip de rețea cristalină; 2) diferența în componentele razelor atomice nu trebuie să depășească pentru aliaje pe bază de fier 9% și aliaje pe bază de cupru 15%; 3) Componentele trebuie să posede proprietăți fizico-chimice de afinitate. Cu toate acestea, aderarea la aceste proprietăți nu conduce întotdeauna la formarea de soluții solide substitutionali cu solubilitate nelimitată. În practică, de regulă, formează o soluție solidă cu solubilitate limitată.
Soluțiile solide pot fi doar o concentrare limitată, deoarece numărul de pori în rețeaua este limitată, iar atomii de component principal sunt stocate la nodurile cu zăbrele.
O soluție solidă substituțională cu solubilitate nelimitată bazată pe componente: Ag și Au, Ni și Cu, Mo și W, V, și Ti, etc.
soluții solide substitutionali cu solubilitate limitată bazată pe componentele: Al și Cu, Cu și Zn, etc.
Soluțiile solide: dizolvarea elementelor metalelor nemetalice ca carbon, bor, azot și oxigen. De exemplu: Fe și C.
fermitate # 150; Această rezistență de penetrare a materialului din suprafața corpului său etalon (cavitație) nu deformabile testat.
Răspândită datorită faptului că nu este necesar modele speciale.
Această metodă de testare non-distructive. Metoda de bază pentru evaluarea calității produselor tratate termic. La judecarea duritatea sau adâncimea de penetrare a penetratorului (scala Rockwell), sau din cea mai mare indentare indentare (metode Brinell, Vickers microduritatii).
În toate cazurile, deformarea plastică a materialului. Cea mai mare rezistență la deformare plastică a materialului, cu atât mai mare duritate.
Cele mai utilizate metode de Brinell, Rockwell, Vickers și microduritate. Circuitele de testare sunt prezentate în figura 3.

Figura 3 # 151; Schema de duritate:
și # 150; Brinell; b # 150; Rockwell; în # 150; Vickers
duritate Brinell
Testul se efectuează pe tester de duritate Brinell (Figura 3a).
Ca un indentorului utilizat călit bilă de oțel cu un diametru de 2,5 D; 5; 10 mm, în funcție de grosimea produsului.
Caracteristica de sarcină P, în funcție de diametrul bilei și duritatea măsurată: pentru oțelul tratat termic si fonta # 150; P = 30D 2. bronz turnat și alamă # 150; P = 10D 2. aluminiu și alte metale moi foarte # 150; P = 2,5D 2.
Durata expunerii. pentru fier din oțel și turnate # 150; 10 pentru alamă și bronz # 150; 30.
Amprenta rezultată este măsurată în două direcții cu o lupă Brinell.
Duritatea este definit ca raportul dintre sarcină P aplicată pe suprafața sferică a amprentelor digitale F:
Termenii standard sunt D = 10 mm; P = 3.000 kgf; = 10 s. În acest caz, duritatea HB Brinell este notat 250, în alte cazuri, condițiile indicate: HB D / P / τ, HB 5/250/30 # 150; 80.
scala Rockwell
Pe baza amprentei în suprafața vârfului sub o anumită sarcină (Figura 3 b)
Indentor pentru materiale moi (până la 230 HB) # 150; oțel diametru bila 1/16 „(Ø1,6 mm) pentru materialele dure # 150; con de diamant.
Incarcarea se efectuează în două etape. Mai întâi aplicat preîncărcare P 0 (CCC 10) pentru contact strâns cu vârful probei. Apoi, sarcina principală F este aplicată 1. pentru ceva timp acționează volumul de muncă global R. După îndepărtarea sarcinii de bază este determinată valoarea duritatea reziduală adâncimea indentare h vârfului sub sarcină P 0.
În funcție de natura materialului folosit trei scala de duritate (tabelul 1)
Tabelul 1 # 151; Cântare pentru duritatea Rockwell
Încercarea de duritate Vickers
Duritatea este determinată de imprimat (figura 3).
Ca indentorului diamant patrulateră piramidă utilizată având un unghi la vârf de 136 °.
Duritatea se calculează ca raportul dintre sarcină P aplicată pe suprafața amprentei F:
De sarcină P este de 5 ... 100 kgf. Diagonala imprimare d se măsoară cu un microscop montat pe instrument.
Avantajul acestei metode este acela că este posibil să se măsoare duritatea oricărui material, produse subțiri, straturile de suprafață. înaltă precizie și sensibilitate a metodei.
Metoda de microduritate # 150; pentru a determina duritatea componentelor structurale individuale, iar faza de aliaj, un strat de suprafață foarte subțire (câteva sutimi de milimetru).
Metoda analoaga Vickers. indentorului # 150; Piramida de încărcare mai mică de amprentare P sunt 5 ... 500 kg:
metoda zgârierea
Diamond con, o piramidă sau o minge este pus un zero, care este o măsură. Atunci când sunt aplicate zgârieturi pe alte materiale și le-au comparat cu o măsură a durității materialului este judecat.
Poate provoca o lățime zero de 10 mm sub o anumită sarcină. valoarea observată pentru sarcina, care dă această lățime.
Metoda dinamică (Shore)
Mingea aruncată pe suprafața cu o înălțime predeterminată, acesta ricoșează la o anumită valoare. Cu cât valoarea de rebound, cu atat mai greu materialul.
Ca urmare a specimenelor dinamice de test de impact cu crestătură specială (GOST 9454) a evaluat vâscozității materialelor și a stabilit tendința lor de a tranziției de la ductil la casant.
viscozitate # 150; capacitatea materialului de a absorbi energia mecanică a forțelor exterioare datorită deformării plastice.
Energia este caracteristică materialului, exprimată în unități de muncă. Vâscozitatea metalelor și aliajelor este determinată de compoziția chimică, tratarea termică a acestora și alți factori interni.
De asemenea, viscozitatea depinde de condițiile în care functioneaza metalul (temperatura, rata de încărcare, prezența ridicatoare stres).
Sistem de aliaj fier-carbon primar cristalizarea începe la atingerea temperaturilor liniei ABCD (linia lichidus) corespunzătoare, și se termină la temperaturi AHJECF linie de formare (linia solidus).
La temperaturi corespunzătoare liniei BC, soluția lichidă este austenita cristalizată. În aliaje având de la 4,3% la 6,67% carbon, la temperaturi corespunzătoare liniei CD, cristalele devin proeminente cementită primare. Cementita, cristalizând din faza lichidă, numită primară. Din punctul B, la o temperatură de 1147 ° C și concentrația de carbon în suspensie 4,3% din eutectic este format, care se numește ledeburită. Eutectică pentru a forma o formulă ledeburită poate fi scris ZHR4,3 A [U + A 2.14 6.67]. Procesul de cristalizare primară a liniei ECF de fier capete formează un ledeburită.
Astfel, structura de fier turnat sub 1147 ° C va fi: hypoeutectic # 150; austenita + Ledebour, eutectic # 150; Ledebour și hipereu # 150; cementita (primar) + Ledebur.
Transformările care au loc în stare solidă, se numesc cristalizare secundară. Ele sunt asociate cu tranziția când este răcit γ-fier in α-fier și descompunerea austenitei.
linia GS corespunde temperaturilor care încep transformarea austenitei în ferită. Sub linia de aliaje GS compuse din ferită și austenită.
line ES arată temperatura de debut a precipitării cementită austenitei datorită reducerii carbonului în solubilitate austenită cu scăderea temperaturii. Ciment, eliberat din austenita, numit cementită secundar.
La punctul S, la o temperatură de 727 ° C și concentrația de carbon în amestec eutectoid austenită 0,8% a fost format constând din ferită și cementita, care se numește perlit. Perlit se obține prin precipitarea simultană a particulelor de ferită și cementită austenită. Procesul de transformare a austenitei în perlită pot fi scrise cu formula A 0,8 P [F 0,03 + 6,67 C].
Linia PQ indică pentru a reduce solubilitatea carbonului în ferita în timpul răcirii și izolarea cementita, care se numește cementită terțiară.
Prin urmare, aliaje care conțin mai puțin de 0,008% carbon (punctul Q), sunt o singură fază de ferită și au o structură netă și aliaje care conțin carbon din 0,008 la 0,03% # 150; Structura fierului tehnic ferita + cementita terțiară și numit.
oțel hipoeutectoide la o temperatură mai mică decât 727ºS au structura de ferita + perlit și clasele hypereutectoid # 150; perlită + cementita ca ochiuri secundar de-a lungul limitei grăunților.
The hypoeutectic fontele în intervalul de temperaturi 1147 # 150; 727ºS asupra răcirii din austenita cementita secundar alocat datorită scăderii solubilității carbonului (linia ES). La atingerea temperaturii 727ºS (linia PSK) austenita, carbonul sărăcit până la 0,8% (punctul S), transformarea în perlită. Astfel, după ce structura de răcire finală hypoeutectic fonta este format din perlită și ledeburită secundar cementita convertit (perlită + cementita).
Structura eutectic fonta la temperaturi sub 727ºS constă din ledeburită convertit. Hipereutectice fonta la temperaturi sub 727ºS constă din ledeburită convertit și cementită primar.
Figura 4: o diagramă de fier-cementita, curba de răcire b pentru aliajul care conține 2,2% carbon
Faza Regula stabilește o relație între numărul de grade de libertate, numărul componentelor și numărul de faze și este exprimată prin ecuația:
unde C # 150; numărul de grade de libertate ale sistemului;
K # 150; numărul componentelor care formează sistemul;
1 # 150; număr de factori externi (factor extern ia în considerare doar temperatura, deoarece presiunea cu excepția efect redus foarte mare asupra echilibrelor fază a aliajelor din statele solide și lichide);
F # 150; numărul de faze în echilibru.
un aliaj de fier cu carbon conținând 2,2% C, numit hypoeutectic fonta. La temperatura camerei, # 150; Perlit + ciment + Ledebour.
tratament izoterm suficientă pentru a obține U8 duritate HB = 150 oțel este recoacere izotermă (Figura 5). Structura după recoacere # 150; perlit krupnoplastinchaty. Când izotermă oțel de recoacere U8 este încălzit la o temperatură de 30-50 ° C mai mare decât punctul A c1 (A c1 = 730 ° C) și după menținerea temperaturii este răcit la 650-680 ° C Structura după recoacere # 150; perlit krupnoplastinchaty.
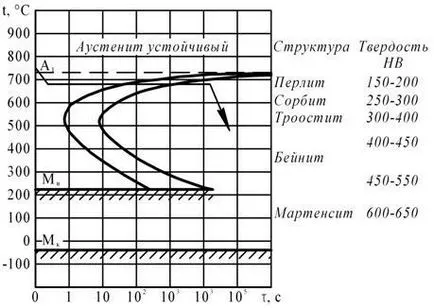
Figura 5 # 150; Figura transformare izotermă a austenitei U8 oțel
transformarea perlitică racim austenitei are loc la temperaturi de la A r1 = 500ºC. În timpul transformării polimorfice apare γ → α-transformarea și redistribuirea difuziv a carbonului în austenită, ceea ce duce la formarea structurii ferita-cementita: A → F + Fe 3 C = perlit.
Austenita concentrația de carbon substanțial omogenă, se descompune pentru a forma cementita și ferită conținând 6,67% C, adică Se compune din două faze având concentrația de carbon diferit. Leading, care apar in primul rand cu faza este carbura (cementita). embrionii sai sunt de obicei formate la limitele granulei de austenită.
Ca rezultat, creșterea particulelor de carbură adiacente acestora volumul austenita este sărăcit carbon reduce stabilitatea și suferă o polimorfic γ → α-transformare. În acest caz, cristalele de ferită nuclea la granița cu cementita, ceea ce facilitează procesul.
creștere ulterioară a plăcilor de ferită duce la îmbogățirea austenitei carbon înconjurător, ceea ce împiedică dezvoltarea în continuare a γ → α-transformare. În acest fel, austenita bogat în carbon provin placa de cementită noi și în creștere a provocat anterior. Ca o consecință a acestor procese de formare și de creștere a particulelor de carburi condițiilor pentru apariția (trombocite), ferita noi și de creștere a cristalelor existente nou create. Rezultatul este un colonial (comun) de creștere a cristalitelor de colonie perlită ferită și cementită constituind.
Pentru a elimina grila grosier de oțel secundar cementita hypereutectoid este supus normalizare.
Normalizarea numit încălzire pro-eutectoid de oțel la o temperatură peste A c3. și hypereutectoid # 150; O cm mai mare la 40-50 ° C, urmată de răcire în aer.
oțel Hypereutectoid după normalizare are o structură de perlită și cementită.
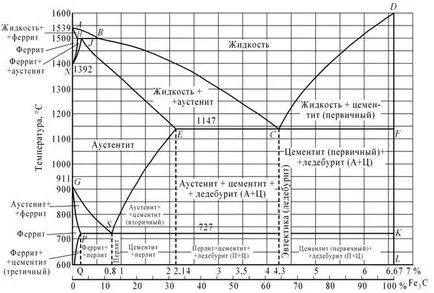
Figura 6 # 150; Diagrama fier-cementita