Secvența de fabricație a matrițelor ipsos uscare calibrare, producția de porțelan și faianță
Formele de gips se usucă în camera (fig. 39), tunelare sau uscator transportor la o temperatură nu mai mare de 70 ° C timp de 16-30 ore, în funcție de dimensiunile matriței la o umiditate reziduală de 5-6%.
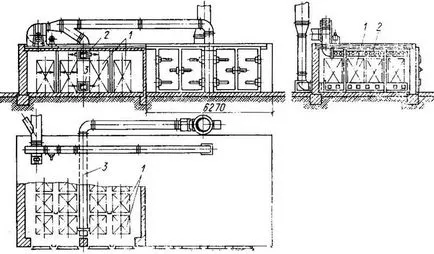
Fig. Schema 39. Camera de uscare pentru matrițe din ipsos
Camera deshidrator este format din două camere, fiecare cu patru rânduri de cuști plasate 1. Sistemul de încălzire și ventilație comun ambelor camere. Refulare duză antet 2 este situată sub camera de tavan și conducta de evacuare 3 în camera inferioară (pe podea). Pentru a reduce costul de uscare uscator de căldură echipate cu un sistem de recirculare (refolosire) a lichidului de răcire. Consumul de energie termică per 1 kg de umiditate evaporată în uscător este 8400- 9240 kJ. Rata recoltând apei este invers proporțională cu umiditatea relativă a lichidului de răcire.
Când uscarea matrite ipsos nou turnate în considerare faptul că o rată mare de lichid de răcire la o temperatură scăzută, este mai bine decât agentul de răcire la temperatură ridicată, cu tirajul insuficient. Uniformitatea formei de uscare are o mare influență asupra rezistenței lor, care crește pe măsură uscarea lor.
Uscarea matrite ipsos la o temperatură de 20-40 ° C, trebuie efectuată suficient de lent, cu o umiditate relativă de aproximativ 50%. Datorită coeficientului ridicat de dilatare termică (17,27 x 10 -6 grade -1) formă este răcită la o temperatură sub 38 ° C, cât mai lent pentru a le împiedica fisurarea.
Formularul suprauscată absorb umezeala intens, atunci când în contact cu ei mase sau alunecare, ceea ce duce la formarea de cruste pe suprafața articolelor, falduri și fisuri. Pacat forma umeda este aspirat umezeala din pulpa sau pastă, astfel lungirea modelele de timp de producție, și articole turnate stick la forma.
New mucegai tencuiala este supus calibrării pe un singur ax de mașini-unelte, necesare pentru obținerea de produse predeterminate dimensiuni și formă exactă. Performanță de calibrare semiautomat matrite ipsos tăvi este 480-720 pe oră la o viteză a axului de 6,1 s -1 și puterea electrică de 1 kW.
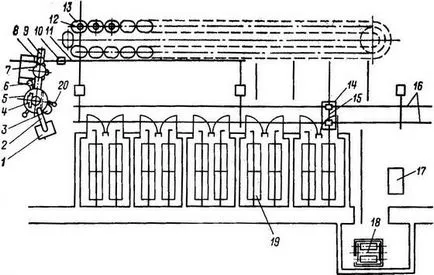
Fig. linie de producție de circuit fabricarea 40. mucegaiurilor ipsos
Schema liniei de producție, înființat la o fabrică de porțelan, ele sunt. M. V. Lomonosova, este prezentată în Fig. 40. Linia include tencuială unitate de preparare soluție închisă bandă transportoare orizontală lung de 26 m, cinci uscătoare de cameră și formulare uscată de calibrare mașină. Operația se realizează nodul de distribuție mortar de apă și gips și vid amestecarea pasta de gips si transportul acestuia la forma umple site-uri.
Lucrările la linia de producție se face în următoarea secvență. Cupă 8 (vezi. Fig. 40) este montat pe căruciorul 9, este alimentat la scara 4. Mânerul 20 inclusiv greutatea, cântărit oala de turnare. Se toarnă în ea cantitatea necesară de apă (în greutate) a distribuitorului 3 și acoperite cu tencuială (în volum) de pulbere de gips dozator buncăr 5. Pulberea de gips este introdus în pâlnia un piept 1 cu ajutorul unui transportor elicoidal 2. găleată umplut alee 6 este alimentat sub vid clopot 7, care este activat după coborârea agitatorul și pompa de vid. După evacuarea clopotul este ridicat și cu o soluție polonic tencuială gata de monorail ridicare 10 este alimentat la transportorul 13. bascularea oalei se toarnă într-o soluție de condensator 12 în timpul deplasării transportorului. Golirea palanul găleată alimentat la locul de spălare reziduuri pastă de gips, apoi ciclul se repetă. Următorul a fost încărcat pentru a forma cărucioare monosină 14 și dirijat în camera de uscare 19, și după uscare a mașinii de calibrare 17. Formulări lifter 18 a servit în atelierul de turnare-laminat la locurile de muncă, folosind pista monorail 16 și transportorul 15.
linie de producție de performanță 1000 forme pe schimb. Pentru a prelungi durata de viață a mucegaiurilor ipsos ale soluției de impregnare este recomandat alaun de potasiu, zinc sau cupru sulfat, borax și proces (imersare) suprafața exterioară a unui alcool polivinilic 2%, urmată de uscare la o temperatură de 60 ° C sau soluție de sodiu sulfit de alcool 50%. Formele sunt, de asemenea, impregnate cu soluții de aluminiu cu densitate borat de 10 ° Baume la 30 ° C în terebentină și colofoniu (raport de greutate 30: 70).