Procesul de producție de fabricație siliciu diagrama cărămidă din materiale ceramice
cărămizi de construcții - aceasta este una dintre acele materiale, fără de care nici un cost, construcția oricărei clădiri sau structuri. Din calitatea de caramida depinde în mare măsură de performanța de proiectare precum și durabilitatea acestuia. De aceea, alegerea materialului de construcție, trebuie să studieze cu atenție unitățile achiziționate.
În acest articol vom descrie în detaliu unul dintre soiurile de acest material - caramida nisip-var, precum și analiza cele mai importante momente ale tehnologiei sale de producție.
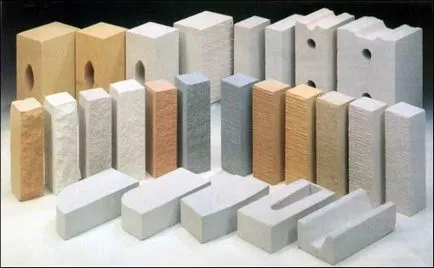
Diferite forme și mărimi silicat blocuri
Prezentare generală
caracteristicile materialului
Cărămidă utilizată în construcția, este o piatră de formă regulată, realizate din materiale special tratate.
Până în prezent, exploatat în mod activ două soiuri de acest material:
- cărămidă roșie ceramica (uneori ca corpolent și gol în interior) - realizate din lut cu diferite componente de stabilizare și de întărire.
- Alb (silicat) - este realizat dintr-un amestec de nisip de cuarț și aer var cernut.
specie silicate este o inventie relativ noua, deoarece compusul din nisip de cuarț cu var într-o structură stabilă a fost posibilă numai după introducerea așa-numitei metode de producție industrie autoclavizat.
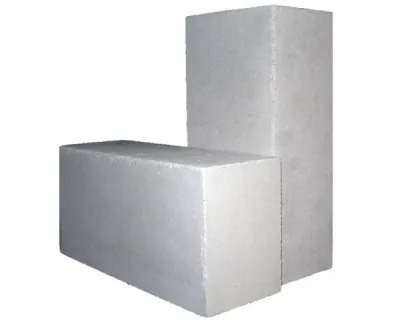
Dublu-var caramida M 150 - una dintre cele mai populare soiuri destul
Acorde o atenție! Nisip și adăugarea de var în amestec pot include pigmenți, rezistent la intemperii și alcaline conținute în șlam. Utilizarea unor astfel de pigmenți pentru a produce specii colorate permite materialului.
Rezultate Blocurile de procesare la temperaturi ridicate au performanțe bune, care este cauza utilizării lor extinse în construcția de diferite structuri.
Beneficiile produsului
caramida nisip-var este astăzi unul dintre materialele de construcție cele mai comune. Motivul pentru aceasta - o listă impresionantă de beneficiile sale:
- În primul rând, materialul este suficient de prietenos cu mediul. Compoziția amestecului de silicat nu include nici toxine sau metale grele, care permite utilizarea completă a blocurilor finite în construcția de case de locuit.
- În al doilea rând, cărămidă are un nivel ridicat de zgomot caracteristici de izolare. Structura internă piatră asigură maximă efectivă de absorbție a sunetului, ceea ce contribuie la o reducere radicală a nivelului de zgomot extern.
- Rezistența mecanică a materialului este, de asemenea, lăudabil. Atunci când sunt combinate cu rezistență la temperaturi scăzute (la fel ca în latitudinile noastre, este important) asigură durabilitatea clădirilor și a componentelor acestora construite din caramida nisip-var.
- Plus Cărămidă silicat de calciu (ca corpolent, și tubulare) este gama largă de produse. Până în prezent, industria produce blocuri de silicat de diferite forme și mărimi. În plus, după cum am menționat mai sus, împreună cu o cerere de culoare alba si este un material - este folosit în principal pentru decorațiuni exterioare.
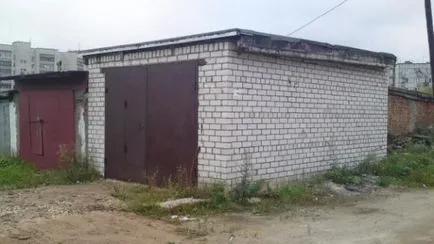
Practicalitatea și ieftinătate - principalele avantaje
Sfat! Dacă sunteți de planificare pentru a construi un zid de cărămidă cu mâinile sale - se consulte cu experți, care vă va solicita cu cea mai potrivită fel, și forma și mărimea preferată.
Simplitatea instalare, operare și întreținere, precum și un preț destul de rezonabil pentru cele mai multe branduri de pe piață sunt, de asemenea, factori care contribuie la creșterea în popularitate.
Contra care trebuie să fie luate în considerare
Împreună cu avantajele unui număr de deficiențe care ar trebui să fie luate în considerare la alegerea materialului de construcție.
Cele mai importante dezavantaje ale blocurilor de silicat includ:
- O masă mare. Caramida cântărește mult. care limitează utilizarea sa în construcția de înaltă creștere. De aceea, acest tip de material este cel mai des utilizat în construcția de clădiri joase (case particulare, vile, clădiri agricole, etc.).
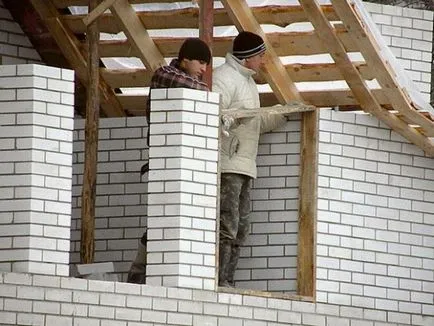
greutate considerabilă restricționează utilizarea în clădire înaltă
- rezistență la temperatură scăzută. Utilizați blocuri de amestec silicat poate fi la o temperatură nu mai mare de 550 0 C. deoarece materialul nu este adecvat, fie pentru coșuri de zidărie, seminee sau placare, etc.
- Susceptibilitatea la săruri de umiditate și sol. Sub influența blocurilor soluțiilor de sol acestea pot pierde puterea, așa că nu le folosesc pentru construirea de plinte.
În ceea ce privește caracteristicile unui material izolator termic, acestea sunt destul de controversate. specii corpolent posedă conductivitate termică semnificativă, dar cărămidă goală la interior oferă destul de un teplosberezhenie decente, deși în detrimentul rezistenței reduse.
tehnologia de producție
Componentele amestecului
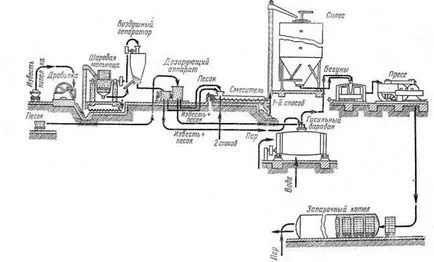
Schema ciclului de producție
Așa cum am menționat mai sus, schema tehnologică a producției de cărămizi ceramice a fost cunoscut de mult timp. În general, aceasta a suferit modificări semnificative, deoarece invenția, pentru că astăzi, la fel ca sute de ani în urmă, blocurile ceramice realizate din lut ars.
Dar producția de materiale de construcție silicat - aceasta este o destul de noua tehnologie. În ciuda faptului că amestecul de nisip-var a început să fie folosit chiar și în cele mai vechi timpuri, caramida reală (blocuri rigide formă fixă) au fost producătoare de abia după 1880.
A fost apoi inginerul german Michaelis a fost brevetat tehnologia de amestec termopressovki nisip și var:
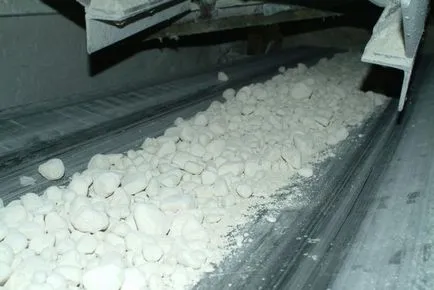
Acorde o atenție! silicat de var ars folosit pentru a face blocuri. Călirea se realizează direct în timpul preparării amestecului silicat.
tehnologie silicat de fabricare în masă
Materia primă pentru producția de blocuri de silicat de tip diferit este o masă așa-numitul silicat. Cea mai comună Instrucțiunea prepararea sa necesită amestecarea a 9 greutate fracție de nisip cernut cu fracțiune de var un aer.
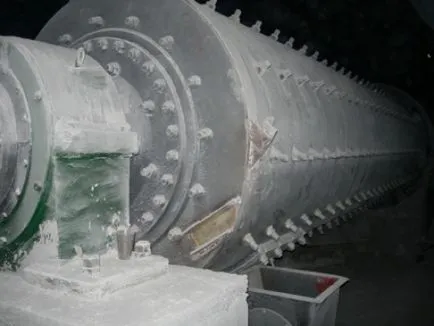
Drum de masă silicat
Până în prezent, producția industrială de cărămizi utilizate două metode de preparare a unor astfel de amestecuri - silozuri și tambur.
- Metoda cilindrului este oarecum învechită și o muncă intensă, deoarece punerea sa în aplicare necesită o cantitate semnificativă de abur la temperatură ridicată.
- La prepararea tamburului mase de silicat de ingrediente uscate sunt puse în mantaua tamburului și se amestecă timp de câteva minute.
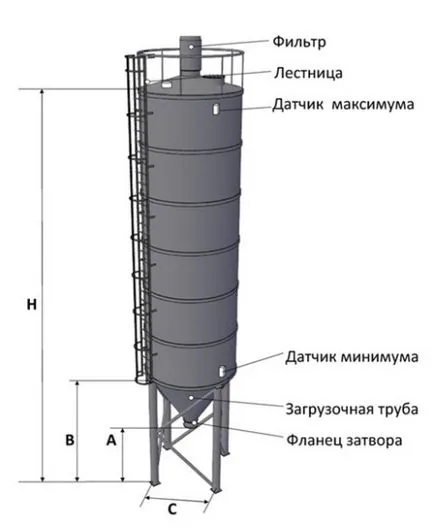
- După realizarea uniformității amestecului este tratat cu abur. Astfel, există o compoziție de hidratare și var stins, care durează aproximativ o oră.
- Metoda Siloz este considerată mai economic, deoarece în cursul perechilor de însilozare este necesară. Cu toate acestea, această tehnologie este mult mai consumatoare de timp.
- Când nisipul însilozate și var alimentat în malaxor unde slăbit și umezită până la omogenizare. Amestecul a fost apoi introdus în coloane verticale - silozuri.
- Silozurile în înălțime și 10 m și un diametru de 3-4 metri înainte de amestec este de 10 ore. În acest timp există nestins.
- De obicei, silozuri echipate cu mai multe secțiuni interconectate care asigură continuitatea procesului de preparare a materiilor prime de silicat.
- După terminarea amestecului silicat proces de călire descărcat din partea de jos a silozului printr-un alimentator special în formă de con.
Indiferent de modul în care s-a obținut masa de silicat, apoi se trece la etapa de presare.
comprimarea brută
Calitatea produselor finite, și anume solide și blocuri de silicat goale, depinde în mare măsură de cât de bine tehnologia va fi respectată atunci când compact-caramida:
- mucegai Presare umplut masa de silicat care este alimentat fie direct din silozuri de alimentare sau de pe banda transportoare.
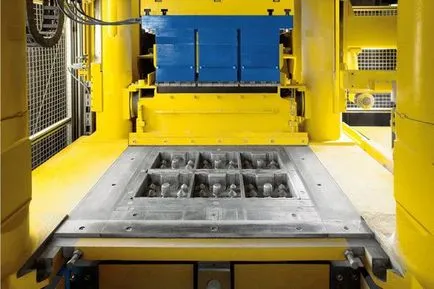
- În unele cazuri, înainte de hrănire amestecul este turnat în buncăr suplimentar, în cazul în care este re-amestecare și umiditate suplimentară.
- mucegai în continuare servit pe echipamente de presare, în cazul în care are loc masa de etanșare. Când compactarea nisipului boabe se apropie unul de altul la o distanță minimă, prin care blocul este scos din substanțial tot aerul și cantitatea de goluri este redus la minimum.
Acorde o atenție! compact Eficacitatea depinde în mare măsură de umiditatea amestecului. Fiecare producție este determinată de acest parametru individual, dar, în general, considerat o valoare acceptabilă a conținutului de umiditate aproximativ 6-7%.
- Presiunea la sigiliu joacă, de asemenea, un rol foarte important. Pentru produsele cele mai durabile, și în același timp, reduce la minimum riscul de distrugere, ar trebui să fie de aproximativ 150200 kg / cm2.
- Compactate cărămidă țaglă împins formulare pe o masă specială. În această etapă, un rol important este jucat de compoziția de umiditate, astfel încât să nu udate suficient de blocuri compacte poate cădea în afară atunci când este împins.
După montarea pe masa, o mașină specială înlătură piesa de lucru și le transferă la o bandă transportoare, de la care, la rândul lor, hrănite la zaparochnye cărucior.
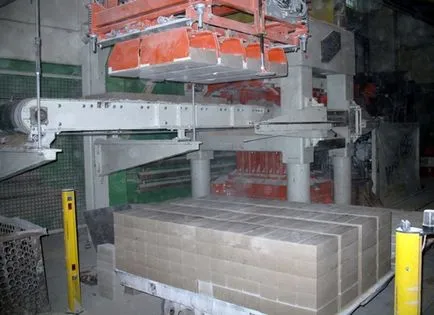
Instalarea pentru depozitarea de prime după presare
autoclavare
Etapa finală a procesului de fabricație a materialelor de construcție - abur în autoclave speciale. Tehnologia modernă autoclavare implică utilizarea unor cărucioare speciale, care permit prelucrarea simultană a unui număr mare de spații de abur fierbinte.
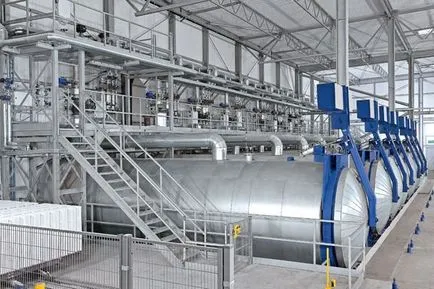
Autoclave pentru aburirea
Acorde o atenție! Pentru a minimiza pierderile de căldură și de a reduce consumul de combustibil, autoclave moderne sunt echipate cu cochilii de izolație termică.
- La primirea cărucioarelor în aparatul autoclavă este închisă și aburul este introdus în ea. Temperatura optimă a aburului este de aproximativ 200 0 C.
- Aburire cărămidă brută se realizează sub o presiune de aproximativ 16 bari. Acest lucru îmbunătățește eficiența de materii prime de prelucrare de abur și de a îmbunătăți performanța produsului finit. De regulă, autoclava este controlată de automatizare, pentru a realiza o mai mare precizie de temperatură și presiune.
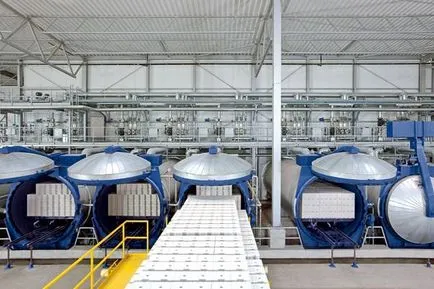
Cărucior care intră digestoarelor
Autoclavare are loc în trei etape:
- Inițial, semifabricatelor alimentate cu abur cu temperatură ridicată, care se răcește treptat, se încălzește cărămidă brută.
- Odată ce temperatura aburului și semifabricatele sunt egalizate, asigură întreținerea automată a unui nivel constant încălzirea autoclavă timp de câteva ore. Acesta a fost în acest interval de timp și are loc reacția de silicat.
- Finală etapă - răcirea preformelor. Temperatura aburului în autoclavă a fost redusă treptat, pentru a minimiza riscul de șoc și crăparea articolelor finite termic.
- Ciclul de funcționare al autoclavei prin abur același lot de cărămizi este de la 10 până la 14 ore. În unele situații, de data aceasta poate fi crescută la 20 de ore.
- In timpul autoclavizare, solidificarea finală se produce un amestec de silicat, după care se deschide dispozitivul și zaparochnoy căruciorului extras din camera.
- În etapa finală, cărămizile descărcare și depozitarea pe tăvi.
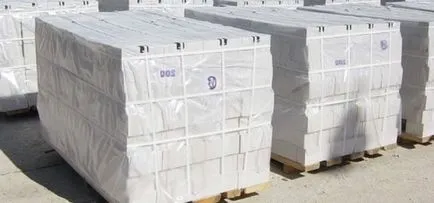
Fotografii de produse finite în stoc
Schema tehnologică de producție descris oferă cărămizi maximiza performanțele sale. Stricte proporții amestec conformitate, recomandările prin apăsarea și controlul temperaturii în autoclavă în condiții de călire sunt necesare produse de calitate de fabricație.