Podele din beton pentru depozite
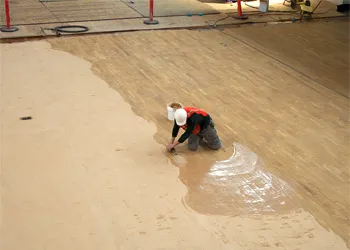
acoperiri din beton sunt utilizate pe scară largă datorită rezistenței sale ridicate la uzură, la un preț relativ scăzut. fabricarea lor este în mod tipic într-un singur proces cu instalarea unui monolit purtător. În funcție de scopul și caracteristicile camerei este determinată de construcția pardoselii de beton.
Atunci când aparatul de acoperire de beton necesar să se ia în considerare strict caracteristici ale bazei, fiind ghidat de laborator independent de cercetare caracteristicile sale. Pentru realizarea unor procese tehnologice de înaltă performanță de acoperire din beton durabilitate aplica suprafață moderne podea durificare folosind amestecuri lichide și uscate, compoziții de ciment polimer, care sunt stivuite pe partea de sus a unui alt strat nefermentate sau „vechi“ de beton de la 5 la 12 mm.
Secvența de operații tehnologice cu un aparat de acoperire din beton cu un strat cementat superior.
1. Suprafața de nivelare.
Folosind subiectul este cel mai înalt punct al bazei de podea. Se specifică grosimea plăcii de beton: tipic 100 mm (monolitului beton) la 150-250 mm (compactarea solului). Trebuie subliniat faptul că podelele din beton de grosime mai mică la salvarea neîndoielnică a betonului nu sunt adecvate, deoarece mai susceptibile de a sparge formarea și degradarea ulterioară.
2. carduri etaj pană.
Marginile cardului (zahvatok) trebuie plasate între rafturi de depozitare prevăzute, și anume pe marginile zahvatok pot forma numărul cel mai semnificativ al neregulilor este deosebit de nedorit în depozitare mare creștere. Lățime zahvatok admisibilă nu mai mult de 4 m, iar lungimea depinde de executarea de lucrări pe pavajul schimbului de lucru.
3. Instalarea Ghid.
Utilizarea nivelurilor optice și cu laser set de ghiduri, cum sunt adesea folosite matrițe metalice, profile tubulare sau canale. Pentru așa-numitele etaje „super slim“ recomandabil să se utilizeze matrițe speciale având o rigiditate ridicată și o margine superioară netedă. Complexe de betonare utilizate în țările occidentale au un dispozitiv telescopic cu un vibrator și emițător cu laser efectuează constant de control al nivelului automat atunci când de stabilire a amestecului de beton. Productivitatea ridicată a acestor complexe (de până la cinci mii. Sq. M pe schimb) elimină necesitatea Guides.
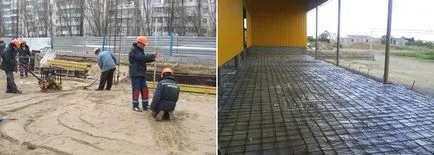
4. armare.
Consolidarea pardoseala de beton se face cu ajutorul unei rețele de armături A -III. Pentru a reduce formarea de fisuri, folosind o armare combinată, adăugând exept beton și fibre de oțel. La instalarea plasei de armare este important să se monitorizeze situația acestora, în scopul de a preveni crăparea de suprafață. Atunci când se utilizează o ranforsare sub formă de particule de fibre metalice din beton (debit 25-40 kg per 1 m3 de beton), nu este necesară instalarea ochiurilor de încadrare. În acest caz, reducerea semnificativă a costurilor forței de muncă, pentru că posibil să se utilizeze o complecși repartitie. Cu toate acestea, în acest exemplu de realizare, trebuie avută grijă pentru a se conforma cu formularea amestecurilor de beton și calitatea compactare a solului.
5. Aparatul cordoanelor sedimentare.
Pentru a preveni formarea de fisuri în podeaua de beton, orificiul de intrare a apei, datorită contracției elementelor de construcție, aranjate cusături sedimentare care separă stratul de pereții clădirilor și coloanelor existente. În acest scop, de-a lungul tuturor pereților (exterioare și interioare) și se potrivesc în jurul coloanelor de bandă de spumă (bandă cu grosimea de 3-5 mm).
6. Livrarea amestecurilor și a distribuției de pătrate sale concrete.
O atenție deosebită trebuie acordată dezvoltării tehnologice de conversie - o livrare la timp și fără probleme a amestecului de beton și distribuția acesteia pe vibratoarelor de adâncime carduri de compactare și șipcile. întreruperi în livrarea neacceptate de beton, în încălcarea structurii sale, diferite grade de plasticitate transportate printr-un amestec, deoarece acestea vor afecta negativ calitatea sexelor. Prin urmare, este responsabilitatea foarte importantă a mixului furnizor și echipate cu tehnologie modernă de amestecare.
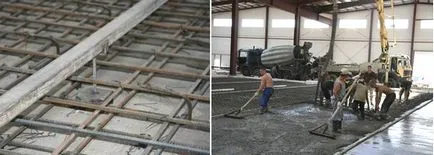
Pentru dispozitiv de pardoseli „super slim“ folosind sape speciale de înaltă calitate, sub control strict și ajustarea geometriei lor. În timp real plasticitate de beton livrate la locul de muncă, va preveni declinul în calitatea de sex.
7. Alinierea amestecului de beton compactat manual.
Profesionalismul și coerența echipei de muncitori - pavele din beton depinde în mare măsură de calitatea pardoselilor din beton, aranjate de tehnologia tradițională - folosind șinele de ghidare și vibratoare. Când de stabilire a pardoselilor din culoarele înguste, fără muncă manuală este indispensabilă. Au folosit aluminiu si sipci de lemn de secțiune dreptunghiulară, profile speciale cu telescopic mânere pentru a netezi suprafața.
8. Expunerea turnat beton.
Temperatura și umiditatea sapei și caracteristicile ambientale ale cimentului de calitate a aerului este timpul de expunere determinată proaspăt turnat suprafață de beton. De obicei, această perioadă este de aproximativ 3-5 ore. În aplicarea tehnologiei moderne de amestec beton vacuum timp de staționare poate fi mai mic de 1-2 ore.
Leading firme străine - producători oferă metoda non-formalizate de determinare a gradului de pregătire a pavaje din beton pentru o prelucrare ulterioară. Ei recomanda începerea următorii pași numai atunci când pantofii lăsați proaspete adâncimea de beton amprenta nu mai mult de 0,4 -0.5 cm.
9. Aplicarea și structura de mortar de armare.
Pe betonul proaspăt turnat de întărire este aplicat manual, primele două treimi din compoziția totală uscată a șarjelor de ranforsare rezistente la uzură, care sunt folosite ca un cuarț graduate, metal, alumină, carbură de siliciu. De asemenea, în acest amestec este ciment Portland și aditivi polimeri care rețin apa ductilitate de acoperire și acordându-i rezistență la apă. În funcție de solicitările mecanice și alte servicii furnizate de funcționarea pardoselilor, este selectată forma amestecul de întărire.
În cazul în care depozitele sunt utilizate cărucioare cu roți monolit din poliuretan, este recomandabil să se folosească de cuarț și umplere corindon (debit - 4-5 kg / mp). Dacă este posibil, utilizați cărucioare cu roți metalice, este necesar să se acorde preferință amestecuri de durificare metalice (consum - 8-12 kg / m²). Ele sunt, de asemenea, folosite și materiale de umplutură, care, cu toate acestea, colorează non-uniform colorate. Numai în termen de una până la trei luni (în funcție de grosimea stratului de beton și condițiile în care se solidifică) culoarea podelei este nivelat.
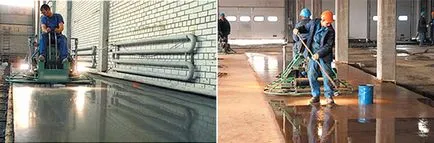
strat întăritor uscat aplicată este suprascrisă (netezite) manual prin intermediul unor șine speciale care sunt profile de aluminiu cu secțiune transversală dreptunghiulară 5x10 cm sau 5x15 cm, prevăzut cu un buton rotativ. Ele sunt, de asemenea, utilizate mistrii la unitatea minimă de viteză. Se aplica discuri cu diametrul de 600, 900 sau 1200 mm. Este de 2-3 trece peste suprafața podelei. Apoi se aplică a treia greutate uscată rămasă întăritor produs și netezirea finală (netezire) primele unități, atunci suprafețele paletelor drisca. În timpul chituire necesară pentru a crește treptat unghiul de înclinare și viteza de rotație a lamelor.
10. aplicarea lacului protector.
Pentru a preveni formarea de fisuri adânci în suprafața podelei din beton finisate, care rezultă din contracția betonului vindecat, este necesar pentru a reduce viteza de evaporare a umidității conținute în acesta. Pentru a face acest lucru fără întârziere, imediat după chituire, cu ajutorul rolelor sau atomizor pneumatice pus pe o suprafață specială podea având o capacitate de reținere a apei, lacuri pe baza de copolimeri acrilici și solvenți organici. Consumul este Lacquer 150-200 g / mp Acest lucru face 0,07-0,12 cm grosime de film care funcționează ca podea șlefuite.
11. rosturi de tăiere contracție.
Mașini speciale echipate cu corindon sau diamant discuri de tăiere produc rosturilor de contracție la o adâncime de cel puțin 2,5 cm etapa de tăiere este de aproximativ 30-40 -. ori grosimea stratului de beton. Cusăturile sunt aranjate în coloane, în funcție de locația, distanțele dintre ele, configurația camerei. Operațiunea trebuie efectuată cel mai târziu după 6 - 8 ore după chitul până fisuri de contracție a început să se formeze.
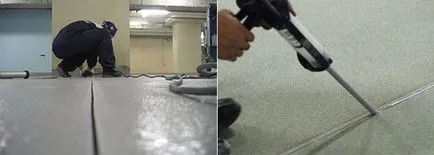
12. Umplerea contracție și expansiune articulațiilor.
În ceea ce contracția betonului pentru o lungă perioadă de timp au format rosturilor de contracție, care trebuie să fie umplut materiale de etanșare. Modul cel mai eficient de a umple rosturile se consideră a le umple cu poliuretan sau material de etanșare epoxidice pentru întreaga adâncime fisuri, deoarece polietilenă cordon de spumă adesea utilizate sunt distruse atunci când operează în trafic intens.
Anumite inconveniente apar în legătură cu faptul că rostuire se poate face numai după timpul necesar, adesea de cel puțin 3 luni. În acest timp, depozitul a pus deja în funcțiune, și este necesar pentru a repara cusături deja în stocul existent.
În legătură cu cele de mai sus se poate concluziona că instalarea de înaltă calitate și podea de beton durabil depinde nu numai de îndemânarea și experiența instalatorilor, ci și pe factori obiectivi - temperatura și umiditatea în cameră, fără schițe, iluminare bună, scurgeri și umezeală. Este necesar să se planifice toate lucrările, astfel încât să nu creeze condiții nefavorabile de stabilire o podea de beton.