Industria, magnitoimpulsnoe modelarea
„Magnitoimpulsnoe modelarea. Plasma laser si electroni de prelucrare cu fascicul de materiale“
Magnitoimpulsnaya Metal Finisare (GIR), - un mod de deformare plastică a metalelor și aliajelor acestora, realizate prin transformarea directă a energiei electrice în energie mecanică direct pe piesa de prelucrat. Deformarea materialului conductor are loc prin interacțiunea câmpului magnetic în impulsuri generate de o sursă externă, cu un curent indus de acest câmp în piesa de prelucrat.
Pentru excitarea elementului conductor de câmp magnetic în impulsuri este utilizat, care este numit un inductor, și poate avea diferite forme.
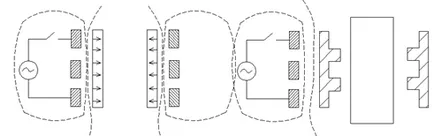
Fig.1. Magnitoimpulsnaya modelarea.
Care trece prin bobina de curent produce un câmp magnetic în jurul acestuia. Dacă acest câmp magnetic, intră în circuitul conductor (2), atunci nu apar curenți turbionari, amplitudinea care este proporțională cu viteza de variație a fluxului magnetic. Interacțiunea curentului turbionar în circuit cu bobina de câmp magnetic extern dă naștere la presiuni mecanice datorită forței ponderomotive.
Pentru a crea o deformare locală între bobina (1) și piesa de prelucrat (2), un butuc metalic (3).
Presiunea exercitată pe piesa de prelucrat un câmp electromagnetic este determinat de relația:
unde B - câmp de inducție magnetică în întrefier; # 956; - permeabilitatea magnetică absolută a mediului.
Presiunea asupra piesei atinge valori # 4 8729 109 N / m2 (la B = 1 MG).
Formarea produselor transportate pe instalațiile de câmp electromagnetic având diagrama schematică
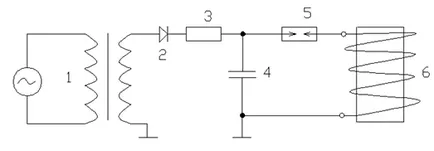
Fig.2. Diagrama schematică a instalației: 1 - transformator de înaltă tensiune; 2 - redresor; 3 - rezistență la baterie; 4 - condensator; 5 - descărcător; 6 - inductor.
Una dintre componentele majore de plante este un inductor de fiabilitate, care depinde de eficiența procesului. Deoarece pentru un inductor suferă efect forță de deformare, este realizată dintr-un material cu rezistență randament ridicat și cu un punct de topire ridicat, cum ar fi cupru, bronz beriliu, oțel, tungsten. rezistența dinamică inductor poate fi crescută prin creșterea masivitatea și a îmbunătăți izolația interturn.
Modurile de prelucrare electromagnetice se selectează pe baza coeficientului de maleabilitate materiale diferite, care este definit prin formula:
unde # 961; - Rezistivitatea electrică a metalului; # 956; - densitatea metalului.
De exemplu, pentru cupru k = 500,000 G / m la oțelurile inoxidabile k = # 3 8729 107 HS / m.
In tratarea pieselor din metal cu rezistență ridicată, ele impun o folie de cupru sau cupru depus electroplacate.
Avantajele modelării puls electromagnetic:
1. procesare de mare viteză, care permite de a modela piese din metal dur și o viscozitate scăzută, nu pot fi supuse la deformare plastică la viteze obișnuite;
2. Absența contactului mecanic între piesa de lucru și inductor, ceea ce face posibilă ștampileze acoperirilor de protecție din metal;
3. relativă simplitate;
flexibilitate 4. Procesul;
5. Cele mai bune condiții de lucru în comparație cu condițiile de lucru la alte metode de piese de formare, etc.
1. Randamentul relativ scăzută datorită pierderii de căldură și de împrăștiere;
2. Complexitatea pieselor cu găuri sau caneluri care împiedică trecerea curentului;
3. inductoare durabilitate scăzută, atunci când operează în câmpurile electrice de intensitate mare;
4. Complexitatea pieselor de grosime mare.
Metoda de procesare a magnitoimpulsnoy utilizată pentru operațiunile de extindere a pieselor metalice cu pereți subțiri de orice formă; sertizare materiale fragile; ștanțare; unirea pieselor metalice cu un non-metal; perforarea dintr-o foaie de metal, etc.
Electro-tratament
prelucrarea materialelor electrohidraulice - această modelare de articole formate din material de tip foaie, folosind unde de șoc dirijate de mare intensitate care apar în lichidul de descărcare electrică pulsată.
Procesarea pieselor apare ca urmare a apariției unei presiuni ridicate în zona de prelucrare, ca urmare a descărcării electrice de înaltă tensiune între electrozii imersate într-un lichid neconductiv. Datorită impulsului de energie undei de șoc răsadurile în jurul canalului de descărcare în mediul de lucru, există o presiune de până la 300 MN / m2. Principalii factori de formare a metodei electro-descărcare sunt:
- șoc hidraulic ultra-înaltă presiune;
- cavitație puternic;
prelucrare electrohidraulică se efectuează în conformitate cu următoarea schemă:
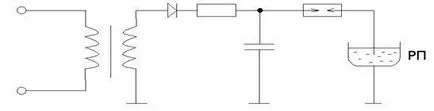
Figura 3. Diagrama schematică pentru prelucrarea electro, în care RP - eclator.
Pentru excitație descărcare traiectoria dorită este utilizat un aranjament diferit al electrozilor, precum și diverse forme de fire scurtcircuitare decalaj interelectrodic.
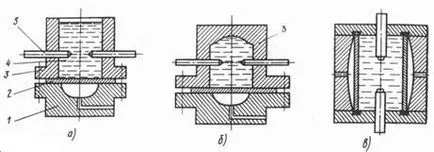
Figura 4. Schema parte stantare electrohidraulic.
Plasma Tehnologia instrumentului, radioapparatostroeniya și metal este folosit ca un jet narrowcasting topitură fierbinte capabil și vaporizează substanțial toate materialele: materialele și nu materiale.
Prin proiectare, torțe de plasmă sunt împărțite în separatoare de acțiuni directe și indirecte.
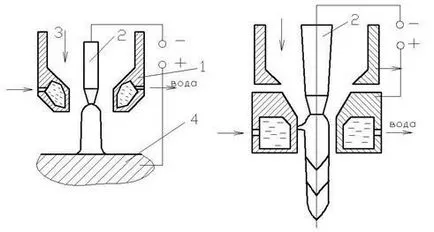
Figura 5. Aparat cu plasmă torță 1 - duză; 2 - electrod de wolfram; 3 - gaz de plasmă de intrare; 4 - produsul; 5 - furnizarea de pulbere de umplere trecere.
Pentru arc de plasmă electrolitică utilizată, prin care este suflat prin gaz cu plasmă duze (argon, azot, aer sau un amestec al acestora). Puterea este furnizată de la sursa de alimentare electrică Plasmatron cu o tensiune de 200-500 V și un curent de 300-400 A. este necesară pentru stabilizarea arcului la jet fierbinte la duza nu a închis și nu se topească, precum și la un accent. Acesta este implementat de gaz cu flux axial sau pereții unei duze răcite redus.
Tratamentul cu plasmă este utilizat în procesele care necesită tăiere mare de căldură concentrată, găuri, micro piercing - și makrosvarka, acoperire, restaurare a pieselor uzate, topirea.
Surfacing strat rezistent la uzură se realizează pentru a îmbunătăți proprietățile de performanță detaliu.
Se aplica materiale pulverulente cu proprietăți speciale - duritate mare, rezistență ridicată la uzură, coroziune - și rezistență la căldură (oxizi de bor sau carburi, wolfram). Detaliile sunt obținute cu un nucleu de materiale de construcții ieftine și în zonele sensibile sunt proprietățile necesare. În mod semnificativ a redus costul materialelor de aliere scumpe. Grosimea stratului poate fi de mai multe mm. Tehnologie: materialul de acoperire este folosit ca o pastă; topește și stratul de sudură sudabile cu materialul de bază mamă. În acest caz, plasma lanterne de acțiune indirectă.
Pulverizare. Pulverizabil Materialul este încălzit în plasmatron. Temperatura substratului în funcție de obiectivul sputtering poate fi variată. Straturi formate din grosime mică - de la câțiva microni la un mm. Pentru a mări aderența stratului pulverizat tind să crească gradul de acțiune chimică a acoperirii pe substrat datorită încălzirii sale sau introducerea straturilor intermediare reactive.
De taiere cu plasma. Avantaje: prelucrează metale până la 100-150 mm grosime, mai mică decât lățimea tăieturii când tăierea gazului, cea mai bună suprafață modificări termice mai mici. Viteza de 0,5-1,5 cm / s, în funcție de grosimea stratului.
Plasma torțe de plasmă de tăiere sunt utilizate în acțiune directă. gaz plasma - argon, azot, hidrogen sau aer. Când microplasma tăiere curent 50-100 O grosime de taiere de 8 mm, lățimea tăiate până la 1 mm.
Caracteristicile generale ale proceselor de interacțiune a radiației laser cu materia
Tratamentul cu laser se realizează cu ajutorul unui fascicul de lumină fin concentrat emisă de către generatorul cuantic optic (laser). Emisia laser este foarte direcțională și monocromatica. Divergența unghiulare ale fasciculului spre rubin este de 30 # 900;, pentru sticlă dopat cu neodim - 10 # 900;.
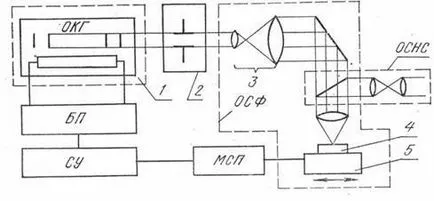
Figura 6. Schema de instalare de prelucrare cu laser.
Dimensiunea minimă la fața locului d0, la care poate fi focalizat raza laser, atinge valori de 1 micron.
Procesul de interacțiune cu laser cu materialul care este prelucrat pot fi împărțite în următoarele etape:
- transfer de lumină energie absorbție urmată de vibrațiile termice ale rețelei a corpului solid;
- încălzirea materialului fără distrugerea, inclusiv de topire;
- distrugerea materialului prin evaporare și descărcare porțiunea sa topit;
- răcirea după încetarea expunerii.
radiație laser de prelucrare a materialului, care este vizualizat utilizând un grafic al îndepărtării specifice substanței # 951; densitatea q flux de lumină absorbită.
Sub îndepărtarea specifică a substanței # 951; Aceasta se referă la masa substanței specifice per unitate de energie incidente.

Figura 7. Dependența îndepărtarea materialului din energia incidente.
La o densitate scăzută de material fluxului luminos este încălzit numai prin radiație. Apropierea valorilor q q0 să ducă la formarea zonei topite la locul de localizare a radiației pe suprafață. Prin urmare, intervalul de valori ale lui q = q0 recomandabil să sudeze materiale. Odată cu creșterea în continuare a procesului de distrugere de material densitate a fluxului luminos începe mai întâi prin evaporare (dacă q0109 W / cm2 mecanism „evaporare“ eșec se înlocuiește cu „exploziv“ și îndepărtarea specifică substanței este redusă cu aproximativ 5 ori.
Relația de mai sus permite să justifice de energie moduri de prelucrare cu laser. Zona de flux este alcătuit tratament q0 suprafață termică a produselor, urmată de încălzire și topire locală. În fluxurile de la q1 la q3, urmată de distrugerea și eliberarea porțiunii topită a materialului se face găuri de tăiere și de foraj.
Pentru a îmbunătăți precizia și calitatea găurilor formate se utilizează materiale de prelucrare multipuls.
Constă în faptul că găurile sunt obținute prin impactul unei serii de impulsuri scurte (0,1-0,2 ms), timpul ciclului este considerabil mai lung timpul de răcire a materialului. Efectul pozitiv al procesării multi-puls se realizează prin:
- îmbunătățirea rezistenței dinamice a materialului pentru scurtarea timpului de șoc termic;
- mai uniformă în ceea ce privește tratamentul continuu al distribuției tensiunilor reziduale pe grosimea materialului.
Când procesarea multi-impuls atinge adâncimea găurilor de 1-5 mm și poate fi de până la 25 de ori diametrul.
prelucrare-fascicul de electroni
de prelucrare cu fascicul de electroni se bazează pe utilizarea fluxului de energie a electronilor suprafețe îndreptate pentru formarea pieselor prin încălzire, topire și vaporizarea materialului în zona de tratament. Pentru tratarea materialelor cu fascicul de electroni, folosind instalații speciale, care creează un puternic fascicul de electroni direcționate. Diagrama schematică a acestui aparat este prezentat în ris.8.3. Principalele elemente ale acesteia sunt ansamblul de catod și sistemul de focalizare și fasciculul de mișcare (Detalii). Tunul de electroni este format dintr-un încălzit catodic 1, focalizarea electrod 14 și o accelerare a anodului 2. Fasciculul de electroni 3 emis de suprafața încălzită a catodului 1 este colectat în fascicul îngust focalizare electrod 14 și accelerată prin diferența de potențial între anod 2 și catod 1. fascicul de electroni îngust dorit dimensiunile sunt utilizate, electrostatice și electromagnetice lentile 4 și diafragma 5. după ce trece prin ele, fasciculul lovește piesa 10 montat pe spațiul de lucru 11. Prelucrarea realizată în camera 12, în care CPNS etsya vid înalt (133 # 8729; 10-6 Pa). Observarea procesului de tratare se realizează printr-un sistem optic 8, un ocular 13, o oglindă semitransparentă 7 și iluminarea 6.
În prezent, există două sisteme principale de control al fasciculului. In primul sistem fasciculul se mișcă pe suprafața piesei de prelucrat, și linia de prelucrare coincide cu traiectoria de mișcare a fasciculului. Mișcarea fasciculului este setat sau computer care controlează jugul deflexie 9 sau dispozitivul de fotocopiere, care constă într-o foto-mască, sistemul de iluminare și amplificatorul fotomultiplicator (PMT). Lumina este amplificată de acesta și, ca un semnal de control care trece prin masca cade pe fotomultiplicatorul este alimentat în sistemul deflectoare. În unele cazuri, spațiul de lucru poate fi mutat pentru un anumit program. In al doilea sistem fascicul trece succesiv toate părțile liniilor la suprafață, și un dispozitiv special deblochează tun de electroni numai în zona tratată.
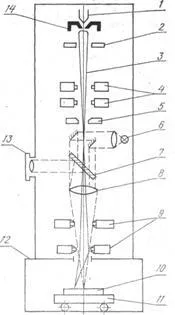
Figura 8. Diagrama schematică de formare a fasciculelor de electroni orientați aparatul.
Atunci când este expusă la un fascicul de electroni pe material, electronii penetrează într-o anumită adâncime # 948;. Valoarea sa depinde de tensiunea de accelerare U și densitatea materialului # 961;:
Odată cu pătrunderea electronilor în materialul din energie este transferată către electroni și nuclee atomice. Cea mai mare parte din energia cinetică a electronilor este transformată în energie termică, porțiunea rămasă este transformată în fotoni de radiație electromagnetică, raze X, radiații și emisia de electroni secundari.
Caracteristicile tehnologice de prelucrare cu fascicul de electroni (performanță, precizie, rugozitatea suprafeței și altele asemenea) sunt determinate în mare măsură de capacitatea echipamentelor (tabelul 1), energia parametrilor fasciculului de electroni, proprietățile materialului prelucrat.
de prelucrare cu fascicul de electroni este aplicat în micromachining dimensionale și sudarea, fascicul fin concentrat de electroni poate obține un diametru al orificiului minim de 0,5 microni și maximum un pasaj - 0,2 mm. Performanța procesului în timpul tăierii, pieselor atinge 1 mm 3 / min, precizia de prelucrare - 2 - 3 microni, rugozitatea suprafeței corespunzătoare clasei 11-lea. prelucrare dimensională este utilizat pentru tăiere și de cusut din materiale semiconductoare, elemente de producție de film și circuite integrate semiconductoare, elemente de memorie de calculator de prelucrare ferită, etc.
Avantajele sudare cu fascicul de electroni sunt după cum urmează: sudură posibile de puritate pentru a obține lățimea suduri de 1 mm sau mai puțin, impactul temperaturii locale, penetrarea profunda si abilitatea de a suda materiale dielectrice. La sudarea nu este material conductor, de exemplu, sticlă, ceramică, aplicată pe suportul pentru probă din două tungsten metalic sau din molibden, care servesc drept anod suplimentar.
Sudarea cu fascicul de electroni este utilizat pentru cipuri montare pe plăcile cu circuite imprimate, cu circuitul și este montarea în interior.
Dezavantajele tratamentului cu fascicul de electroni trebuie să includă complexitatea unităților de proces, costul lor ridicat și necesitatea de a lucra într-un vid înalt.
În plus, apariția inevitabilă a hard raze X necesită o protecție specială și respectarea precauții stricte de siguranță.
· Bazele tehnologiei de industrii majore :. La ora 2 pm, Partea 1: Textbook. Manual pentru școli / IV Chentsov, IA