Corporate University
TPM - întreținerea eficientă a echipamentelor
TRM (gestionarea totală a producției) este un sistem de acțiuni planificate ale muncitorilor, inginerilor, reparatori ca o echipă, care vizează maximizarea eficienței echipamentelor sale prin întreținere preventivă pe tot parcursul ciclului de viață.
TRM - este un instrument pentru a îmbunătăți performanța generală, hardware întreprindere ca un singur sistem.
TRM - este o muncă de echipă, un fel de continuare a sistemului 5S.
Fără TPM este imposibil să se introducă orice calitate built-in, nici sistemul „tocmai la timp“ și Kanban său instrument sau dispozitive Poka-Yoke (protecție împotriva erorilor) devine lipsită de sens SMED (schimbare rapidă).
Mai mult decât atât, în unele cazuri, TPM poate fi cel mai important instrument al „lean manufacturing“. De exemplu, dacă produc produse pe echipament automat. Iar pentru un număr de întreprinderi autohtone până când, din păcate, este important nu numai, dar, de asemenea, singurul. Și introducerea tuturor celorlalte elemente ale „Lean Manufacturing“ Apoi trece prin dezvoltarea și diseminarea TPM.
Scopul TPM - este crearea companiei, care caută în mod constant să limiteze și să îmbunătățească eficiența sistemului de producție integrat.
Înseamnă să capăt este stabilirea unui mecanism, care să cuprindă locuri de muncă directe, are drept scop prevenirea tuturor tipurilor de pierderi ( „zero accidente“, „prejudiciu zero“, „căsătorie la zero“) de-a lungul întregului ciclu de viață de producție.
Pentru a atinge obiectivul implică toate departamentele: inginerie, afaceri, management, și mai presus de toate, productiv.
În realizarea obiectivului tuturor personalului implicat - de la liderul suprem la „prima linie“ angajatului.
Dorința de a realiza „pierderi zero“ este pusă în aplicare în cadrul unor grupuri mici conectate ierarhic, în care sunt unite toți angajații.
Ce poate compania TPM?
Scopul implementării TPM, așa cum sa menționat mai sus, - pentru a realiza cea mai mare eficiență și un sistem integrat de producție. Cu alte cuvinte, pentru a obține cel mai bun rezultat posibil în producție otnosheniiobema (producție - P), calitatea produsului (calitate - Q), costul (cost - C), calendarul de alimentare (de livrare - D), locuri de muncă de securitate (siguranță - S) și inițiativa personalului (moral - M), cu un consum minim de resurse umane, materiale și.
Tabelul 1 prezintă datele medii pentru mai multe companii japoneze - câștigătorii Premiul TPM caracterizează rezultate tangibile pe care le-au realizat, precum și efectul intangibil al introducerii acestui sistem.
Înainte de apariția TPM se credea că în natură planta este un „teren de reproducție“ a celor trei „K“ (cu această literă în limba japoneză a început cu cuvintele - „murdărie“, „condiții dificile“, „pericol“).
Ceea ce elimina pierderile de: Timpul petrecut pe hardware-ul de depanare.
Principala parte a TPM este cooperarea operatorilor și reparatori, cu participarea activă a managementului în domeniul detectării precoce și de prevenire a problemelor și controlul asupra stării echipamentului.
1. Este necesar să se dezvolte un limbaj simplu de înțeles de către operatori și nu necesită o pregătire specială a acestora și, în același timp, suficient de informativ pentru reparatorii (de exemplu, zgomote descrieri calitative standardizate necaracteristice ale motorului, și așa. D.).
3. O parte importantă a TPM este o documentație sistematică a datelor privind eficiența totală a echipamentului. În cazul în care aceste date sunt menținute pentru o lungă perioadă de timp, de multe ori acestea indică o scădere a performanțelor cu mult înainte cauzele care stau la baza acestui declin va duce la o oprire completă de producție. Este logic pentru a face procesul de documentare a acestor date cât mai simple și împovărătoare. În cele mai multe cazuri, suficiente pentru a lua în considerare numai 3 raport:
a) disponibilitatea, performanța și randamentul produsului, definit după cum urmează:
Disponibilitate = timpul de funcționare teoretic / timpul disponibil în ansamblul său;
Performanță = capacitatea reală / capacitate teoretică;
Produs Randament = randamentul de produse din prima încercare / productivitatea reală.
TPM implică îmbunătățirea eficienței sistemului de producție prin eliminarea tuturor pierderilor la mai eficient ca munca umană și utilizarea de echipamente, energie, materii prime și instrumente. De obicei, industriile producătoare emit 16 pierderi de specii. Această cifră poate fi extinsă pentru fiecare întreprindere în parte.
În conformitate cu o astfel de abordare pentru evaluarea eficienței sistemului de producție nu este valorile locale sunt utilizate în TPM, cum ar fi factorul de încărcare al echipamentelor, precum și rata de eficiența globală care să reflecte toate tipurile de pierderi. Relația dintre eficiența echipamentelor de ansamblu și tipuri majore de pierderi, precum și procedura de calcul a coeficientului de eficiența generală a echipamentului.
Conform conceptului TPM, un obstacol major pentru utilizarea eficientă a echipamentului constă din două tipuri de defecțiuni: cauzează echipamente de închidere și să conducă la o abatere de la cursul normal de muncă și, prin urmare, implică o căsătorie sau de alte pierderi.
Spargerea - un „vârful aisbergului“, care creste din defectele ascunse. Cum ar fi praful, particulele de murdărie lipirea uzura materialului, slăbirea, backlash, coroziune, deformare, fisură, vibrații, etc ..
Defectele ascunse se acumulează și se susțin reciproc, având ca rezultat se produce ruperea.
Practica TPM distinge două grupe de motive pentru defecte latente nu i se acordă o atenție din cauza.
Primul își are originea în psihologia umană. defecte ascunse nu sunt percepute de ochi, ei nu acorde atenție, ei nu ar exista, și, prin urmare, nu-și dau seama că acestea sunt cauza eșecului.
Al doilea grup de motive este legat de echipamentul în sine și să stabilească procedurile sale de funcționare. În special, nu se iau măsuri pentru eliminarea fenomenelor care provoacă defecte latente (praf, murdărie, m. P.). Echipamentul este adesea proiectat astfel încât orice defecte ascunse nu pot fi detectate, pentru că totul este închis capace și capace, sau dificil din cauza accesului dificil de purjare, gresare, strângerea șuruburilor.
Apariția defectelor ascunse se deteriorează starea echipamentului, rezultând o deviere de la starea sa normală. Prin urmare, TPM a dezvoltat un sistem pentru a identifica defectele ascunse și să aducă echipamentul la starea normală.
„Zero ruperi“ TPM se realizează prin eliminarea treptată, punerea în aplicare sistematică și continuă a celor cinci grupe de activități:
- crearea condițiilor de bază pentru funcționarea normală a echipamentului;
- respectarea condițiilor de funcționare a echipamentului;
- restabilirea uzurii normale;
- eliminând lipsa structurală (cauzată de proiect) a echipamentului;
- a îmbunătăți abilitățile operatorilor, reparații și întreținere, ingineri de proiectare.
Trebuie subliniat încă o dată că, în punerea în aplicare a acestor activități implicate în mod absolut toate diviziile companiei.
STADIUL echipamente de înaltă performanță, în conformitate cu conceptul de TPM pus deja în etapa de proiectare. Acesta a fost inițial să fie fiabile, sigure, ușor de utilizat și de întreținut, un consum economic de resurse.
Conceptul central al TPM - costul pe parcursul întregului ciclu de viață - costului ciclului de viață (LCC) - include costul echipamentului și costul de funcționare pentru întreaga durată de viață. Alegerea echipamentelor și metodelor sale de operare este realizată astfel încât să se reducă la minimum costul echipamentului și costul de funcționare pentru întreaga durată de viață.
În TPM, ca, într-adevăr, și în tot ceea ce privește calitatea, este esențial să nu numai rezultatul introducerii acestui sistem, dar, de asemenea, procesul de implementare sale. Mai mult decât atât, în cazul în care implementarea este organizată în mod corespunzător, iar beneficiile așteptate aproape sigur nu va fi obținut.
Acest lucru explică atenția sporită fiind acordată dezvoltării TPM în secvențe de acțiune și o structură organizatorică pentru a promova acest sistem cu adevărat eficient.
În efectuarea de reparații majore și îngrijire corespunzătoare, chiar și pentru instalațiile de producție existente pot crește funcționalitatea și precizia la 20-30%. Cu alte cuvinte, sistemul primar este eficient pentru a opera echipamentul, pentru a stabili care ar trebui să înceapă imediat. Și numai în prezența și gradul de dezvoltare a unui astfel de sistem depinde de faptul dacă societatea va fi în măsură să scoop toate dispozițiile echipamentelor existente și achiziționarea de noi greșeli și pentru a evita pierderile care apar în mod inevitabil, în absența unui astfel de sistem.
În ciuda faptului că baza TPM sunt, în ideea generală, simplă, dezvoltarea sa necesită o mulțime de efort și de timp - de la 3 la 10 ani, deoarece implică o schimbare fundamentală în filosofie și psihologie a fiecărui lucrător și întregul set de relații între angajații companiei . Cu toate acestea, deoarece experiența companiilor care au implementat acest sistem, rezultatele sunt exact tipul de schimbare și acum reprezintă unul dintre principalul avantaj competitiv asupra lumii
dificultăți de punere în aplicare
- Această incapacitate de a vedea întregul proces cu eliberarea factorilor de limitare în ea.
- este inerent în sistemul contabil al dorinței pentru optimizarea locală a anumitor operațiuni, uneori, în detrimentul creșterii capacității întregului flux, și a lucrătorilor salariale de eficiență.
- Aceasta nu dorește să delege autoritatea de management pentru cei care cunosc cel mai bine tehnica, care funcționează, etc.
Domeniul de aplicare al cererii prioritare:
În condiții moderne, atunci când nu numai producția, ci și un birou plin de echipamente sofisticate, aplicabilitatea TPM este aproape universală, chiar dacă TPM este încă nu ca 5C, o condiție prealabilă pentru utilizarea tuturor celorlalte metode de fabricație slabă. Potrivit experților, cele mai multe dintre utilizarea TPM poate aduce la procesul de fabricație.
aplicații anterioare: Efectul economic TPM, de asemenea, ușor de amestecat cu alte instrumente Lean efect economic, deși TRM în general mai puțin frecvente decât 5C. În special, progresele substanțiale realizate în aplicarea producătorilor TPM de aluminiu, cum ar fi un producător global №1 lider Alcoa și Rusal pieței românești.
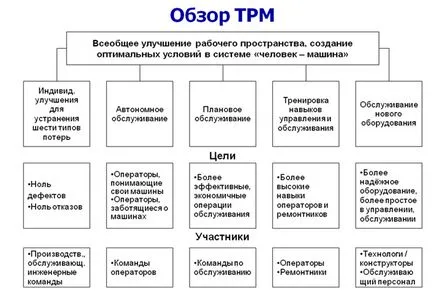